This is the place for the best construction news
Talk.Build delivers the best and latest construction news and in-depth analysis, shaping your understanding of the ever-evolving building industry. This is the best construction news with updates daily. Even better - check out The Feed for construction news in real time from across the globe.
Here's what sets us apart:
- Groundbreaking construction News: Dive deep into the future of construction with coverage of groundbreaking technologies, industry trends, and policy insights.
- Latest construction news: React swiftly to market shifts and policy changes with instant access to breaking construction news impacting the entire sector.
- Informed construction news decisions: Make data-driven choices with our comprehensive coverage of landmark project announcements.
- Tailored Content: Discover construction news relevant to your area of expertise, whether you're a contractor, architect, engineer, or simply a construction enthusiast.
- Streamlined Experience: We cut through the clutter, delivering construction news bites that matter most to you.
- Extensive Archive: Explore hundreds of ongoing construction news stories and utilize our search bar to find specific topics.
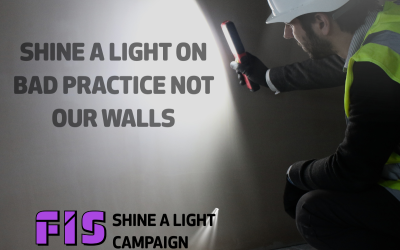
FIS shines a light on bad practice
Finishes and Interiors Sector (FIS) is taking a stand against poor behaviour in the supply chain. Members working in the housebuilding sector have raised concerns about unfair snagging practices on...
Read more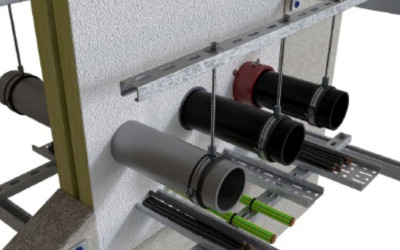
PFKG demands higher standards for MEP service penetration seals
Critical vulnerable areas in UK building safety have been identified by the Passive Fire Knowledge Group (PFKG). As a result, the group is now warning that a widespread reliance on untested or...
Read more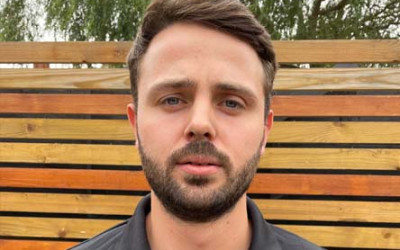
Charlie Anderson highlighting Ambar Kelly’s unrivalled expertise
As a company that leads the high-risk building (HRB) industry in innovation and shines a spotlight on emerging talent, Ambar Kelly is proud of the level of dedication and professionalism shown by its...
Read more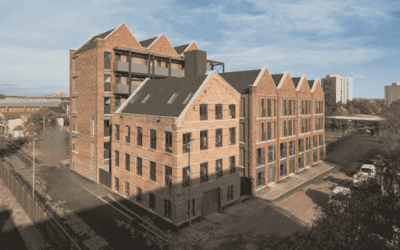
IG Masonry Support’s role in blending heritage with modern living
The Warehaus Ancoats development in Manchester represents a thoughtful blend of historical preservation and contemporary residential design.
Read more
Smart counting as Doka brings AI to the yard
In today’s construction industry, unlocking the full potential of digital transformation isn’t just an option, it’s essential. Doka is leading by example with a proprietary AI solution that automates...
Read more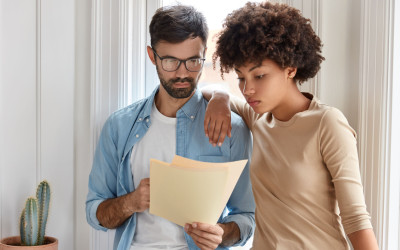
Pulse Fibre doubles down on price certainty
With Ofcom regulations having been introduced to stop inflation-linked price rises in broadband contracts, Pulse Fibre is proud to reaffirm its long-standing commitment to fixed pricing. While some...
Read more