Talk.Build - for the best Commercial Construction Blogs
Looking for the best construction blogs to stay ahead of the curve in the ever-evolving built environment? Talk.Build is your ultimate destination with thousands of different commercial construction blogs to choose from, with more added nearly every day. We serve as a vibrant online forum, to help foster knowledge and exchange views between seasoned industry veterans, emerging talents, and passionate construction enthusiasts.
Check out our extensive Commercial Blog Library: Dive into our expansive library featuring thousands of commercial construction blogs, meticulously categorized and continually updated with fresh content. Diverse Subject Matter: Explore a comprehensive range of topics spanning project management, safety regulations, sustainable construction practices, and cutting-edge building technologies. Expert-Driven Insights: Gain invaluable knowledge from industry leaders who share their practical experience with materials, tools, construction techniques, current design trends, and successful business strategies.
Check out The Feed for construction news in real time.
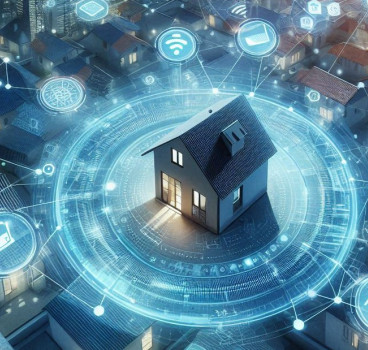
BEMS - the perfect fit for the UK’s retrofitting programme
While the Future Homes Standard (FHS) is exacerbating the need for property developers and house builders to incorporate energy efficient and sustainable technologies and materials into new build...
Read moreHow Sustainable Drainage Systems (SuDS) are changing UK construction standards
For decades, drainage in UK construction has largely relied on traditional pipe systems designed to move rainwater quickly away from homes and roads into sewers. But with climate change bringing...
Read more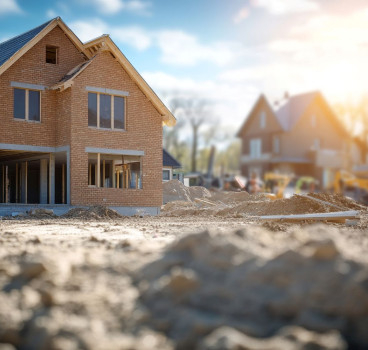
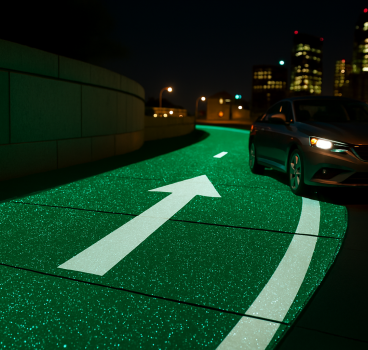
Why glow-in-the-dark concrete is a material for the future
Concrete is the backbone of modern civilisation and is one of the most widely used man-made materials on Earth, but for all its strength and versatility, concrete has never been thought of as...
Read moreGermany’s construction market still stalling at the bottom
Germany’s construction market continues its prolonged slump. While June 2025 saw a modest 7.9% rise in residential building permits compared to the previous year, this uplift follows rock-bottom...
Read more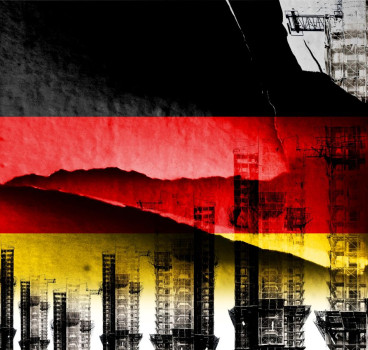
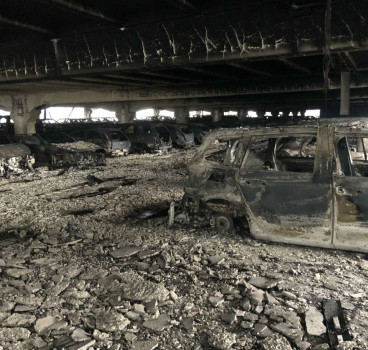
The forgotten impact of the Kings Dock Car Park Fire on Liverpool’s growth and Economy
Last month, I attended the Local Government Association (LGA) Conference in Liverpool on behalf of the Business Sprinkler Alliance. Whilst I should be reflecting on the conference and discussions...
Read moreWhy the Building Safety Regulator is a necessary but challenging direction for the industry
Following the tragic events at Grenfell Tower in 2017 and Dame Judith Hackett’s subsequent inquiry, the Building Safety Act (BSA) was introduced across England and Wales in 2023. Through this, the...
Read more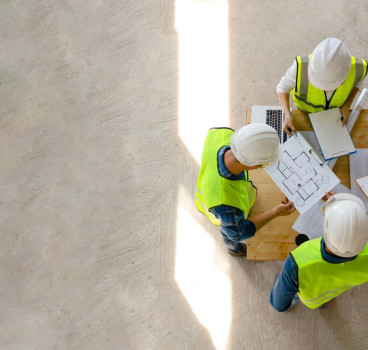
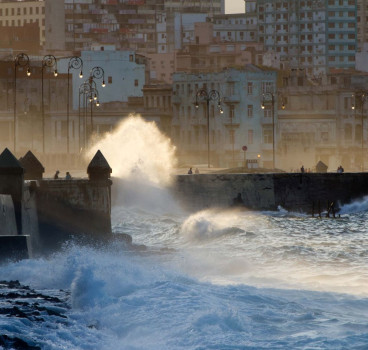
Building for a warmer, wetter and less predictable future
The conversation about sustainability in the construction industry has for too long been dominated by the phrase “green building.” It has become a shorthand for energy-efficient offices, homes with...
Read moreWhat will happen when we lose the forgotten building trades?
Across the world, there are trades that once defined the built environment, but now exist on the edge of extinction. Stonemasonry, lead working, traditional timber framing, decorative plasterwork and...
Read more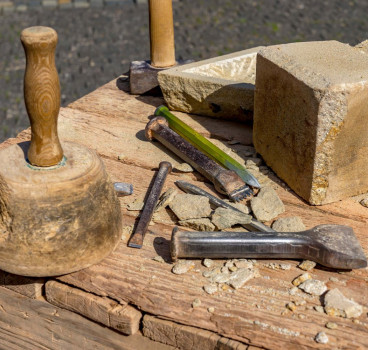
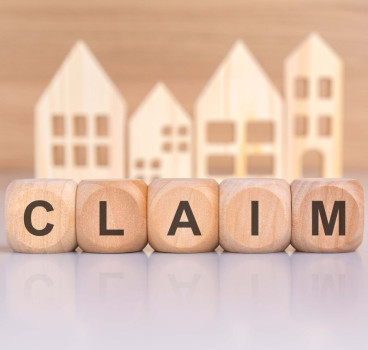
The future of construction insurance as it adapts to climate change and AI
The construction insurance sector is entering a period of rapid change. Two forces are driving it more than any others - the accelerating impact of climate change and the rise of autonomous machinery...
Read more