Talk.Build - for the best Commercial Construction Blogs
Looking for the best construction blogs to stay ahead of the curve in the ever-evolving built environment? Talk.Build is your ultimate destination with thousands of different commercial construction blogs to choose from, with more added nearly every day. We serve as a vibrant online forum, to help foster knowledge and exchange views between seasoned industry veterans, emerging talents, and passionate construction enthusiasts.
Check out our extensive Commercial Blog Library: Dive into our expansive library featuring thousands of commercial construction blogs, meticulously categorized and continually updated with fresh content. Diverse Subject Matter: Explore a comprehensive range of topics spanning project management, safety regulations, sustainable construction practices, and cutting-edge building technologies. Expert-Driven Insights: Gain invaluable knowledge from industry leaders who share their practical experience with materials, tools, construction techniques, current design trends, and successful business strategies.
Check out The Feed for construction news in real time.
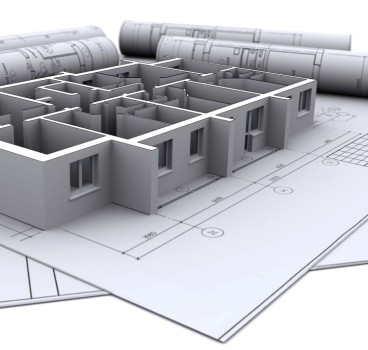
How micro-construction is delivering high-tech solutions for small-scale projects
The construction industry, historically defined by soaring high-rise buildings and vast infrastructure, is now undergoing a quiet revolution. A fast-expanding market segment, known as...
Read moreHow traditional construction procurement undermines innovation
The construction industry has never liked change. While many things contribute to this, one of the most significant and often overlooked factors – and one that holds back innovation – is the...
Read more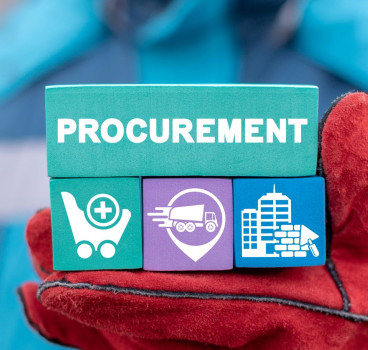
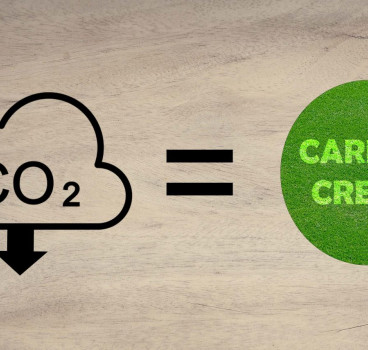
Why carbon offsetting in construction Is a deceptive practice
The global construction industry continues to be under increasing pressure to address its substantial environmental footprint. As a major contributor to greenhouse gas emissions, responsible for a...
Read moreHow gaming technology is changing the construction industry
The construction industry, often perceived as traditional and slow to adopt new technologies, is undergoing a quiet but profound transformation. This evolution is being driven, perhaps surprisingly,...
Read more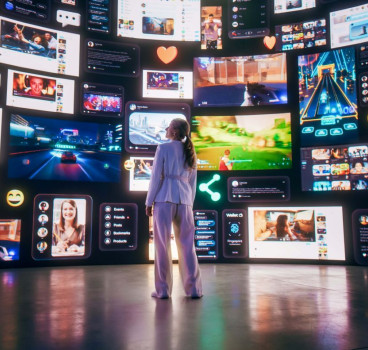

Temporary migrant labour in construction and the unspoken realities
The global construction industry frequently relies on a workforce that often remains invisible to public scrutiny - temporary migrant labour. Beyond the official statistics concerning legal status,...
Read moreWhy do construction site inductions remain rooted in the past?
The construction industry – is slow to change and it’s not the first time I have said this. Among the challenges we continue to face is the site induction, which stands out as a prime example of an...
Read more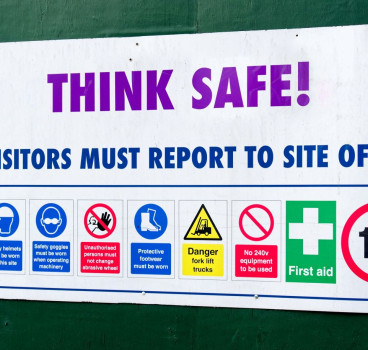
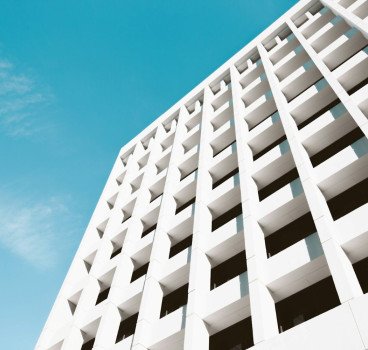
Designing for Disasters -Innovations in Hurricane and Seismic-Resistant Construction
The global population is on the rise. Natural disasters are also becoming more common, forcing people to buy or build in disaster-prone areas. If you act proactively, you can help ensure their safety...
Read moreUnderstanding the problem of “Ghost Projects” in construction forecasting
The construction industry operates on forecasts. Companies meticulously track their tender pipelines, project prospects and confirmed orders, using these projections to inform critical business...
Read more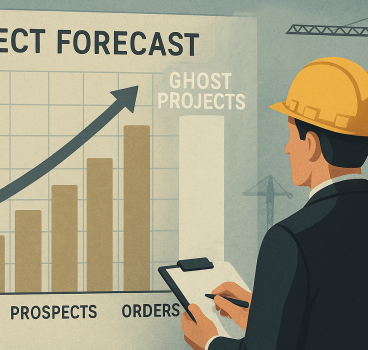
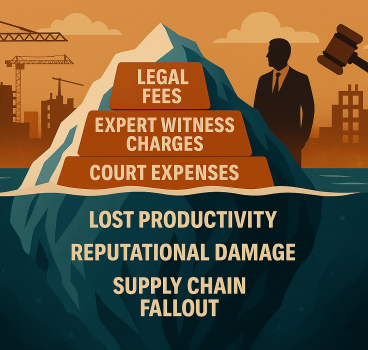
The true economic cost of construction disputes
Disputes are an almost inevitable, albeit undesirable, feature of modern construction. When such disagreements escalate to formal dispute resolution mechanisms, particularly litigation, the immediate...
Read more