Why do construction site inductions remain rooted in the past?
The construction industry – is slow to change and it’s not the first time I have said this. Among the challenges we continue to face is the site induction, which stands out as a prime example of an operational bottleneck frequently stuck in an outdated time loop, resembling practices from the 1990s rather than the digital age. The inefficiencies inherent in many current induction procedures could be changed using modern digital tools which can fundamentally streamline safety protocols and enhance productivity from the moment a worker sets foot on site – but for some strange reasons we seem reluctant in many cases to use this technology, writes John Ridgeway.
A typical construction site induction, even today, often begins with a familiar scene - a queue of new arrivals, a stack of paper forms and a site manager or supervisor attempting to deliver a comprehensive briefing. This manual, often a paper-based, process is fraught with inefficiencies and inherent limitations.
The most immediate and tangible drawback of traditional inductions is the sheer amount of time they consume. Each new worker, visitor, or delivery driver requires individual processing. This can involve filling out multiple forms, watching lengthy video presentations in a communal space and participating in verbal briefings. For large projects with high worker turnover or multiple deliveries throughout the day, these repeated inductions create significant delays.
Time spent in a makeshift induction room is time not spent on active project work. This directly impacts productivity, delaying the start of tasks and contributing to project schedule slippage. The cumulative effect of numerous small delays, multiplied across hundreds or thousands of personnel over a project’s lifecycle, represents a substantial, unquantified economic drain.
The quality and consistency of information delivered during manual inductions can also vary wildly. A site manager delivering a briefing might inadvertently omit critical details due to time constraints, fatigue, or the sheer volume of information. Videos might be outdated or generic, failing to address site-specific hazards. Paper handouts can be incomplete or go unread. This inconsistency jeopardises safety, as workers may not receive all necessary information pertinent to the unique risks of that particular site. Relying on a human to manually cover every detail for every person is inherently prone to error and oversight.
Limited engagement and retention
Sitting through a lengthy, passive presentation or filling out numerous forms can lead to disengagement. Workers, eager to commence their tasks, may tune out important safety messages or simply sign off on documents without fully comprehending their contents. Information overload can result in poor retention, meaning critical safety rules or operational procedures are quickly forgotten. An induction that fails to effectively convey and reinforce vital information is not fulfilling its primary purpose of preparing personnel for a safe and productive day.
Furthermore, paper-based records are inherently difficult to manage, store, and retrieve. Ensuring all necessary signatures are collected, tracking expiry dates for certifications and verifying competency can be an administrative nightmare. Audits become cumbersome and quickly identifying who has completed what training or holds which qualification becomes a time-consuming manual search. This lack of centralised, easily accessible data increases administrative overheads and complicates compliance management.
In short, the sheer volume of paper consumed in manual induction processes represents an unnecessary environmental footprint. From printed forms to information handouts, the waste generated contradicts the industry’s broader push towards sustainable practices.
The solution to these archaic practices lies squarely in the adoption of modern digital tools. Such technology can transform site inductions from a bureaucratic hurdle into an efficient, engaging and highly effective gateway to site operations.
Digital platforms enable pre-induction processes. New personnel can complete much of the administrative and informational components before arriving on site, using their own devices. This includes uploading certifications, watching site-specific safety videos, reading policies and completing comprehension quizzes from their home or office. This significantly reduces time spent on site for administrative tasks, allowing workers to hit the ground running upon arrival. Remote access to induction materials ensures they can be reviewed at a convenient time and location, improving information absorption.
Interactive and Engaging Content
Digital platforms facilitate the use of rich media beyond simple videos. Interactive modules, 3D site walkthroughs, augmented reality (AR) overlays illustrating hazard zones and gamified quizzes can transform the learning experience. Workers can engage actively with the content, making it more memorable and effective. For instance, a virtual tour of a complex area of the site can highlight specific risks in an immersive manner, far more impactful than a static image or verbal description. This interactive approach ensures higher engagement and better retention of critical safety information.
Digital induction systems can also automate the entire record-keeping process. Once a worker completes their induction, their details, certifications and completion status are instantly logged in a centralised, secure database. This eliminates manual data entry, reduces errors and ensures that all records are easily retrievable for audits. The system can automatically flag expired certifications or incomplete training modules, ensuring full compliance at all times. This automation frees up administrative staff to focus on more strategic tasks rather than paperwork.
Furthermore, digital platforms guarantee consistent information delivery. Every worker receives the exact same, up-to-date briefing, regardless of when or where they complete it. This eliminates human error and ensures that all personnel are working from the same foundational knowledge base regarding site rules and safety protocols. The system is infinitely scalable, able to handle a single new arrival or hundreds simultaneously without compromising quality or efficiency.
Digital systems provide real-time data on induction completion rates, common areas of misunderstanding (through quiz results) and certification status across the entire workforce. This analytical capability allows site management to identify systemic issues in training or communication, enabling targeted interventions and continuous improvement of safety protocols. For example, if many workers consistently fail a particular question on scaffolding safety, it indicates a need for clearer communication or additional training in that specific area.
Ultimately, the primary benefit of digitalising inductions is enhanced safety. Better engagement leads to better retention of safety information. Consistent delivery ensures no critical details are missed. Automated compliance checks mean only qualified and fully inducted personnel are active on site. This holistic improvement in how safety information is conveyed and managed directly contributes to a safer working environment, reducing incidents, injuries and the associated human and financial costs.
The broader digital transformation
Modernising site inductions is not an isolated fix - it is a critical component of a broader digital transformation within the construction industry. The data collected during the induction process can be integrated with other digital platforms, such as project management software, workforce management systems and safety management tools.
For instance, a worker's digital induction profile can automatically link to their daily time tracking, ensuring that only inducted personnel can clock in. Their competency records can feed into task assignments, preventing unqualified individuals from undertaking specific roles. Digital induction platforms can also serve as a central hub for ongoing communication, pushing out real-time safety alerts, updated method statements, or weather warnings directly to workers' devices.
This seamless integration fosters a truly connected site environment, where information flows freely and efficiently. It supports a proactive approach to safety and productivity, moving away from reactive problem-solving. Furthermore, by embracing such technologies, construction companies can enhance their professional image, attracting new talent who expect modern, digitally enabled workplaces. For a generation accustomed to intuitive digital interfaces, an archaic paper-based induction can be a significant deterrent.
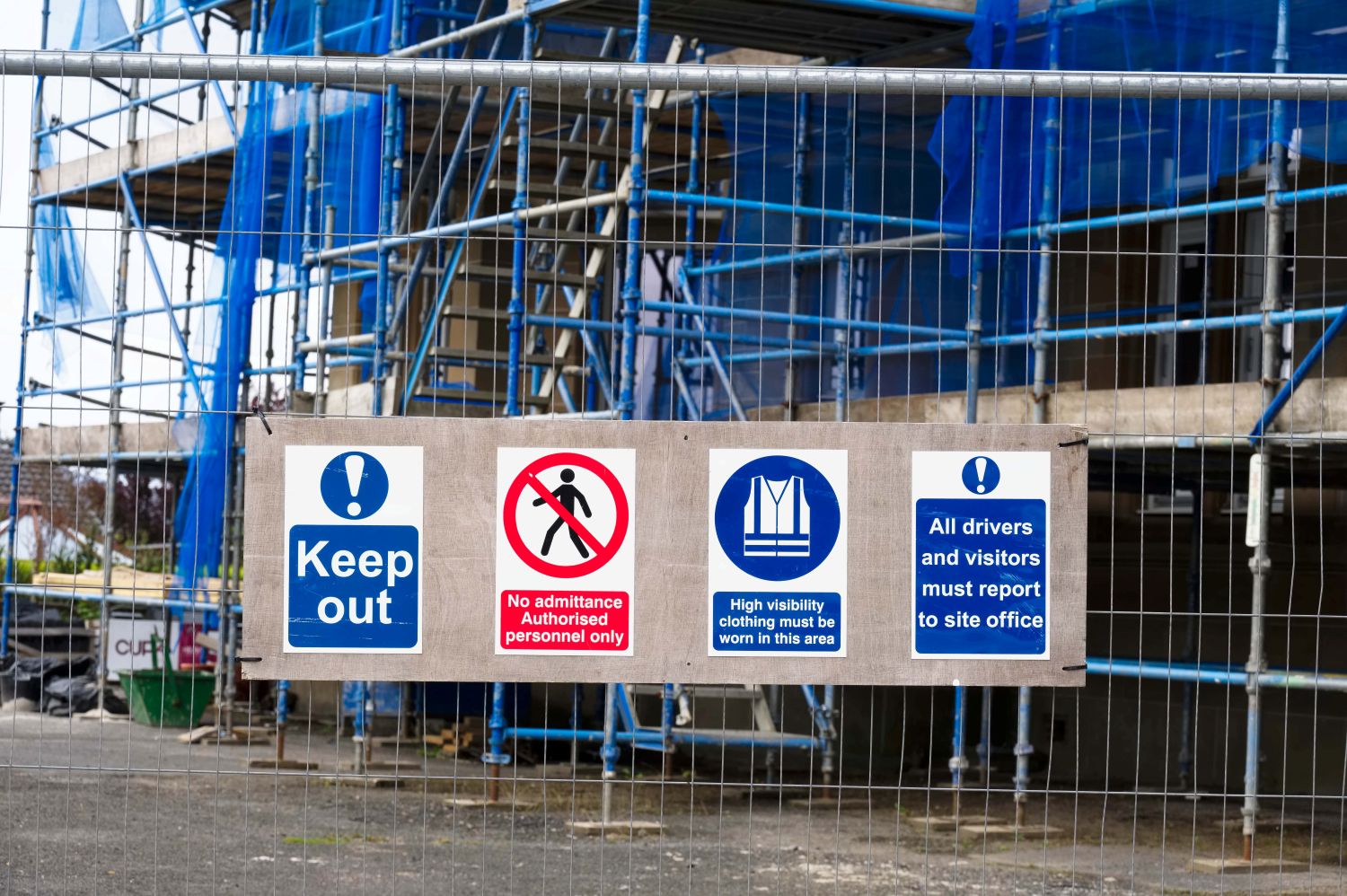
However, the transition from outdated, manual induction processes to sophisticated digital systems requires more than just technological investment - it demands a cultural shift. Companies must overcome inherent inertia, resistance to change and the perception that "the old way works fine."
Leadership commitment is paramount. Senior management must articulate a clear vision for digital transformation, emphasising the safety, efficiency, and commercial benefits of modernising inductions. Pilot projects can demonstrate the immediate advantages, building internal champions and showcasing success stories. Training and support for site personnel are crucial to ensure smooth adoption of new digital tools. It is also important to select user-friendly platforms that are intuitive for all levels of technical proficiency.
Initial setup costs for digital systems might be perceived as a barrier, but these investments must be viewed through the lens of long-term return on investment. The cost savings from reduced administrative burden, decreased time lost to induction, lower incident rates and improved productivity far outweigh the upfront expenditure. The investment is in a safer, more efficient, and more competitive future.
The construction industry's site induction processes are, in many instances, remnants of a bygone era. Their reliance on manual, paper-based methods lead to significant time consumption, inconsistent information delivery, poor engagement and cumbersome record keeping. This archaic gateway to the construction site directly impacts productivity and compromises safety outcomes. The solution lies in a decisive move towards digital transformation. By embracing remote pre-induction, interactive content, automated record keeping, and real-time data analytics, companies can fundamentally streamline the induction process. This modernisation not only enhances safety and productivity from day one, but also serves as a critical step in building a more efficient, technologically advanced, and appealing construction sector. The time to upgrade the industry's front door is long overdue.
Additional Blogs
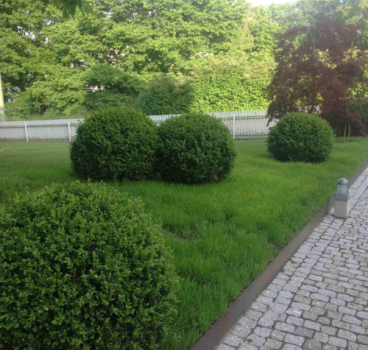
Why healthy soil is the hidden key to quality homes
Across countless new housing developments, a hidden problem is undermining quality and driving up customer complaints - and most housebuilders will never see it coming. The issue is not the homes...
Read moreThe fight for facades or why M&E must shape early design decisions
With sustainability and energy efficiency, not to mention decarbonisation, increasingly taking priority during building design, MEP engineers and architects are coming into conflict as part of an...
Read more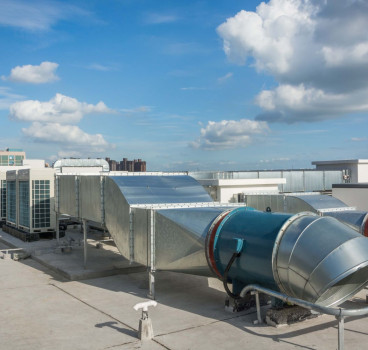
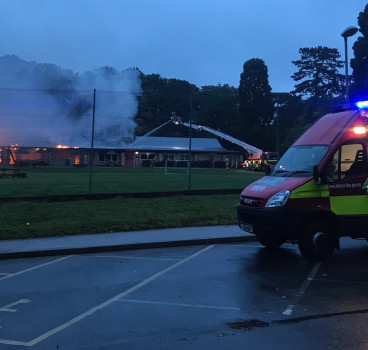
Back to school and the same old story on fire safety
We are about to start another school year and once again, we find ourselves having the same discussion about fire safety guidance for schools. The last attempt to revise Building Bulletin 100 (BB100)...
Read more