LKAB and Forterra to produce recycled calcined clay to replace cement
A partnership between LKAB Minerals, part of the international mining and minerals group LKAB, and building products manufacturer Forterra, is pioneering the use of recycled calcined clay as an alternative to traditional cement in construction.
The production of cement is responsible for up to 8 percent of the world’s CO2 emissions. Addressing this challenge, the industry is looking at new technology, carbon capture and the use of Supplementary Cementitious Materials (SCMs) that are viable at industry-scale. Calcined clay is one such option to replace cement. It has significant potential to scale-up at speed and therefore offers a cost-efficient solution for the industry.
“At LKAB Minerals we are looking to develop new products and applications that support increased material efficiency, sustainable production and support critical uses and the green transformation – this is a perfect example of that and I am very excited about our UK and Construction team activities and plans” says David Högnelid, Vice President Minerals, LKAB.
To create the calcined clay products, Forterra’s brick waste from its Kings Dyke factory is crushed and delivered to LKAB Minerals. This process not only reuses by-product materials but also reduces the need for energy-intensive clinker production. Perhaps most importantly, calcined clay increases concrete’s strength by reducing the porosity of the material. In this innovative approach, the calcined clay is based on recycled brick waste, further reducing carbon emissions compared to primary clay-based materials, and offering circularity.
Steve Handscomb, Managing Director of LKAB Minerals UK and responsible for driving this development comments “The traditional manufacturing and materials industries face a great challenge to meet our own environmental and Governmental targets. We have to work harder than other less energy intensive industries, and need significant investments to upgrade equipment. We are committed to playing a role in the transition. In fact, we are already a significant producer of GGBS which is another recycled cementitious replacement material, and in the Minerals Division,45% of the minerals we sell are from recycled sources or by-products”.
The construction of the production line at LKAB Minerals’ plant in Flixborough is underway, scheduled to start production in June 2025. A third-party verified Environmental Product Declaration (EPD) is in progress to provide customers with accurate environmental impact and C02 figures. Calcined clay will add to the portfolio of LKAB Minerals’ products as cement alternatives including GGBS and Gypsol, an anhydrite-based floor screed.
Additional news
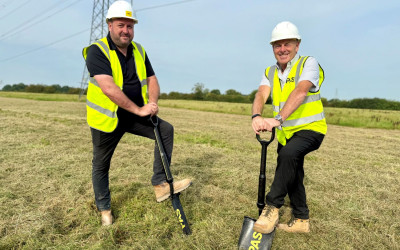
PAS NW awarded major Wain Homes development
PAS NW Ltd is proud to announce its appointment as civil engineering delivery partner on Wain Homes’ significant new residential scheme in Cottam, Lancashire. This landmark development - one of the...
Read more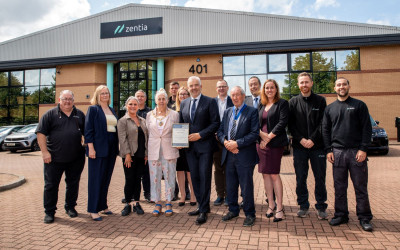
Zentia celebrate 100 years of manufacturing excellence
Zentia, a leading ceiling solutions manufacturer, is proud to announce a major milestone in its history: 100 years since the original company was first registered in the UK. With a rich heritage as...
Read more