Insulation board reduces the challenge of Part L compliance
Progress often comes at a price. In respect of the Part L amendments, this may relate to parties throughout the supply chain having to adopt new behaviours and practices to achieve compliance with the uplift in energy standards.The introduction of the Future Homes Standard (FHS) in 2025 will further strengthen the legislation, which is designed to create more sustainable homes and buildings.
Achieving Part L (Conservation of Fuel and Power) compliance is a pathway to meeting the FHS’ requirement for new homes built from 2025 to produce 75-80% less CO2 than homes built under current regulations. However, a recent survey by construction consultants, Harwood Building Control, revealed that 55% of architecture and building design professionals found responding to the upcoming FHS ‘challenging or extremely challenging’. If so, then delivering the low-energy homes the UK needs to achieve net zero in 2050 could become problematic, to say the least. Therefore, it’s important we get our house in order regarding Part L compliance prior to taking the next legislative step.
Swapping Old-for-New Building Methods Key to Achieving Compliance
Design-wise, new practices are emerging in line with the need for thermally-efficient new housing. For example, gone are the days when architects focused on the energy performance of individual building elements to create compliant, comfortable homes. Current best practice dictates a holistic approach, which takes into account a building’s entire composition – from its elemental junction details to its service and energy provision – as being key to designing homes that perform as impressively as they look.
Part L legislation means there is more to consider at the building design stage. This includes the type of building materials used, which are integral to meeting regulation energy standards, This could instigate a further behavioural change; one that has had a detrimental effect on building performance for longer than is acceptable, involving specified products or materials being swapped for cheaper-but-inferior replacements at the construction stage. If such product changes are to be made, they must be approved by the architect following a recalculation of energy values to ensure there is no material impact to the overall design.
Fabric-First Considerations and Thermal Benefits of PIR
As outlined in Part L amendments, a fabric-first approach to building design – in conjunction with renewable technologies – is fundamental to achieving compliance. High-quality insulation makes a significant contribution to the process, which prioritises the thermal achievements of structural elements, particularly walls, floors and roofs. Due to its lower thermal conductivity and higher thermal resistance in comparison to other insulative materials such as mineral wool, Polyisocyanurate (PIR) insulation is ideal for fabric first design. Despite its slim composition, PIR offers lambda values as low as 0.022. This gives it greater flexibility in respect of its application, allowing designers more freedom to attain aesthetic aims without comprise to thermal performance.
Up to 30% of a building’s heat loss can be caused by thermal bridging, demonstrating the value of insulation that remains dimensionally stable and does not sag or slump. Such is the case with PIR. As an example of how PIR maximises performance in respect of heat flow resistance, it requires a 100mm-thick PIR board to attain a 4.5 R-value. In comparison, 153mm of glass wool is needed to achieve the same result.
An effective thermal insulation strategy is also crucial for renewables to work effectively. Items such as heat pumps have an important part to play in achieving building compliance, but their performance should be supported with a robust fabric-first approach that utilises PIR insulation within the design.
A PIR Board with Performance Plus Points
Excellent thermal performance, durability and usability, with an interlocking tongue and groove feature that makes for tight, moisture-resistant fit; Eurowall® + adds a new dimension to PIR performance. The 10mm air gap resulting from a 90mm Eurowall® + board’s ability in helping to achieve a 0.18W/m2K U-value in 100mm masonry cavity walls is a significant asset. It makes installation an easier, less labour-intensive process for bricklayers, which is a benefit when budget constraints are in place.
Available in 90mm, 115mm, and 140mm thicknesses, Eurowall® + has several other plus points that make it the ideal rigid full-fill PIR insulation board for creating homes that meet Part L compliance and achieve desired levels of style and comfort for the occupier. These include:
- Obtaining higher thermal performance within conventional 100mm, 125mm and 150mm cavity wall sizes
- Eliminating the need for the taping of general board joints due to its tongue and groove feature
- Having two distinct faces to assist installers in fitting boards the right way round
- Increasing protection against wind-driven rain, as well as improving air tightness
Eurowall® + has instigated a change in PIR design and installation. It’s a change for the better for designers and specifiers in need of a product that makes achieving Part L a less challenging prospect.
For more information on how Eurowall® + can benefit your next building project, click here
Additional news
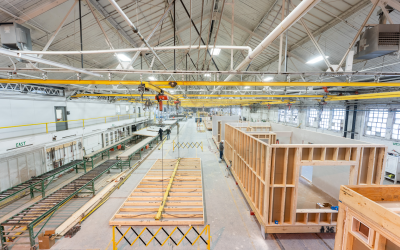
Global Prefabricated Buildings Market Poised for Unprecedented Growth
Market Intelo's comprehensive 2033 market research report unveils transformative growth trajectory driven by digital innovation, sustainability mandates, and rapid urbanization across global markets....
Read more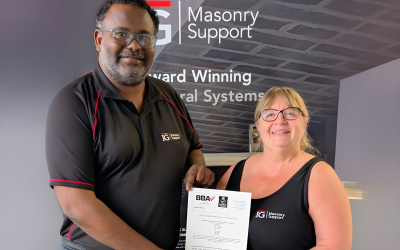
IG Masonry Support achieves independent ISO14001 Accreditation
IG Masonry Support, a market leader in innovative masonry support systems, has announced it has secured ISO 14001:2015 Environmental Management System certification, marking a significant... |