The evolving landscape of heavy construction
The world of heavy construction is undergoing a significant transformation, driven by a combination of technological advancements, sustainability concerns, and a relentless pursuit of efficiency. One significant challenge in particular – to reduce the environmental footprint while maintaining operational power and efficiency – is starting to gain traction – as the industry strives to go green, as it seeks to replace traditional “greenhouse gas polluting” diesel-powered equipment, writes John Ridgeway.
Suddenly, everyone is talking about hydrogen fuel cells, a technology which offers a promising solution for powering heavy construction equipment in a cleaner and more sustainable way.
Hydrogen fuel cells are similar to batteries, but instead of storing electrical energy, they convert hydrogen gas and oxygen from the air into electricity through an electrochemical reaction. This process produces water vapour as the only significant emission, making it a clean alternative to diesel engines. The fuel cells power electric motors, which drive the machinery, eliminating exhaust emissions and reducing noise pollution on construction sites.
Hydrogen fuel cells create near-zero emissions, significantly contributing to combating climate change and improving air quality. Compared to diesel engines, hydrogen fuel cells offer higher efficiency, translating to improved fuel economy and potentially lower operating costs.
The absence of combustion engines leads in turn to significantly reduced noise pollution, creating a more pleasant and safer work environment for construction workers and the surrounding communities – and the added bonus - hydrogen refuelling times can be comparable to diesel refuelling, minimising downtime and maintaining operational efficiency.
However, converting to hydrogen is not without its problems. At the time of writing, the infrastructure for hydrogen refuelling stations is still under development, particularly outside major cities – in fact it is virtually non-existent. This will limit the widespread adoption of hydrogen-powered equipment in the short term.
Hydrogen-powered equipment typically has a higher upfront cost compared to diesel alternatives. However, long-term fuel cost savings and potential government incentives may offset this initial cost difference – and as with any new technology, safety protocols and training are crucial for handling and storing hydrogen fuel and will have to be introduced before the technology is more widely adopted.
While still in its early stages of adoption, hydrogen-powered construction equipment is being actively tested and implemented in various projects worldwide. JCB, one of the world’s leading manufacturers, has developed and tested hydrogen-powered excavators and backhoe loaders, demonstrating the feasibility of this technology in real-world applications.
Komatsu, in collaboration with Cummins, is developing hydrogen-powered mining trucks aimed at reducing emissions in the mining industry. National Highways, the UK government agency is also exploring the use of hydrogen-powered construction machinery for infrastructure projects, aiming to achieve net-zero emission targets within their operations.
As the technology matures and infrastructure expands, hydrogen fuel cells have the potential to become a game-changer for the heavy construction industry. Continued research, development, and collaboration between manufacturers, governments, and energy providers are crucial for overcoming existing challenges and paving the way for a cleaner and more sustainable future for construction projects around the world.
The Rise of Electric and Hybrid Construction Equipment
In the bid to eliminate diesel, there has also been a surge in the development and adoption of electric and hybrid construction equipment. This shift towards electric-powered heavy plant and equipment is gaining momentum in the construction industry, driven by concerns about environmental impact, regulations on emissions, and advancements in battery technology. However, while offering several benefits, this technology also faces limitations that need to be addressed for widespread adoption.
Electric equipment offers a significant advantage in terms of emissions reduction. They also generally require less maintenance compared to internal combustion engines, leading to reduced operational costs in the long run. Additionally, with the potential for lower electricity prices compared to diesel fuel, depending on the region, electric equipment can offer cost savings over time.
Electric motors can deliver instant torque, translating to improved efficiency and responsiveness compared to diesel engines. This can be particularly beneficial for applications requiring quick acceleration and precise control, such as operating cranes or forklifts.
However, the main challenge with electric equipment is battery range. Construction projects often cover large areas, and current battery technology may limit the operational time of electric machines before requiring a recharge. Additionally, the infrastructure for recharging heavy equipment is still in its early stages of development, especially outside major cities.
The initial cost of electric equipment is also typically higher compared to diesel alternatives. This is primarily due to the cost of batteries, which are still undergoing technological advancements to become more affordable. As heavy construction equipment requires a significant amount of power to operate, the local electrical grid may not have the capacity to support widespread adoption of electric equipment without upgrades and infrastructure improvements.
Despite the limitations, the future for electric heavy machinery looks promising. With ongoing advancements in battery technology, including increased capacity and faster charging times, the operational range and efficiency of electric equipment are expected to improve significantly. Additionally, investments in charging infrastructure development are underway, making it easier to recharge equipment on construction sites.
However, to fully replace diesel-powered equipment, significant challenges still remain. Collaboration between equipment manufacturers, energy providers, and policymakers is crucial to develop cost-effective solutions, invest in infrastructure expansion and create regulations and incentives that support the transition to a more sustainable construction industry.
In the meantime, hybrid construction equipment, combining an electric motor with a traditional diesel engine, also offers improved fuel efficiency compared to solely diesel-powered equipment. They can also operate in electric-only mode for tasks that don't require full power, further reducing emissions and noise – and this could well be the right solution in the short term.
The Integration of Autonomous Technology
Autonomous construction equipment, also known as driverless or robotic equipment, is also gradually making its way onto worksites. These machines utilise various technologies, including sensors, cameras, and Lidar (Light Detection and Ranging), to navigate their environment and perform tasks with minimal human intervention.
They deliver increased safety by removing workers from potentially hazardous environments, improved productivity by operating continuously without breaks, and enhanced precision in tasks such as excavation and grading.
That said, the high cost of technology, regulatory hurdles, and potential job displacement concerns are some key challenges that need to be addressed before widespread adoption becomes possible.
The Power of Data and Analytics
The construction industry is increasingly embracing data and analytics to optimise operations and improve efficiency. This involves collecting and analysing data from various sources, such as sensors embedded into equipment, where they monitor engine performance, fuel consumption, and real-time location data.
So, we can see that the future of heavy construction is brimming with exciting possibilities. As technology continues to evolve and sustainability concerns become paramount, the industry will witness further advancements in environmental concerns, automation and data utilisation. Companies that adapt and embrace these trends will be well-positioned to thrive in this ever-changing landscape – and the future looks good.
Sources:
https://www.jcb.com/en-us/campaigns/hydrogen
https://www.komatsu.com/en/newsroom/2023/gm-komatsu-collaborate-on-hydrogen-fuel-cell-mining-truck/
https://www.aem.org/news/5-reasons-construction-jobsites-are-going-electric
https://www.aem.org/news/5-reasons-construction-jobsites-are-going-electric
https://www.constructionbriefing.com/news/autonomous-construction/8011035.article
https://www.autodesk.com/design-make/articles/autonomous-vehicle-technology-in-construction
Additional Blogs
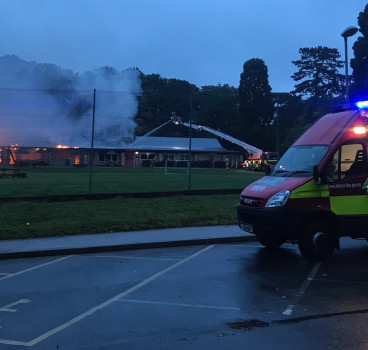
Back to school and the same old story on fire safety
We are about to start another school year and once again, we find ourselves having the same discussion about fire safety guidance for schools. The last attempt to revise Building Bulletin 100 (BB100)...
Read moreBEMS - the perfect fit for the UK’s retrofitting programme
While the Future Homes Standard (FHS) is exacerbating the need for property developers and house builders to incorporate energy efficient and sustainable technologies and materials into new build...
Read more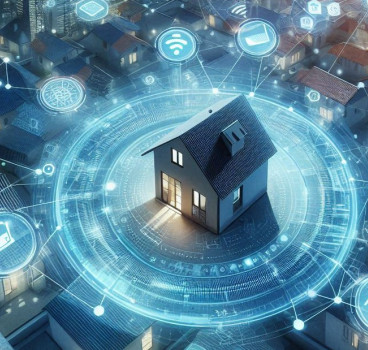
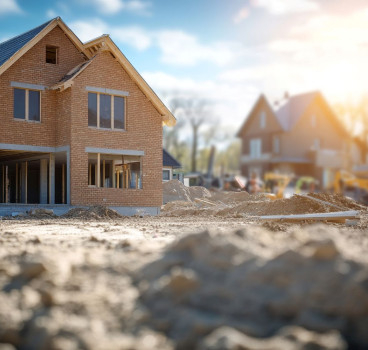
How Sustainable Drainage Systems (SuDS) are changing UK construction standards
For decades, drainage in UK construction has largely relied on traditional pipe systems designed to move rainwater quickly away from homes and roads into sewers. But with climate change bringing...
Read more