Why modular offsite construction will continue to boom in the UK
According to number of recent reports, the UK construction industry will need some 400,000 new workers every year until 2021 to meet the demand for new building projects.
If the figures are correct then it is going to be a tough call, which in turn means looking at alternative methods of construction. Fortunately we have a thriving industry in the UK for building offsite and most experts reckon that this will be the answer if the building industry is to prosper in the future.
Recent surveys in America, where they are facing similar skills shortages, revealed that the amount of project work using off site prefabrication almost tripled between 2010 and 2016 and it is a similar story here.
In the UK, Your Housing Group has recently signed a £2.5bn joint venture with a Chinese state-owned construction company to build 25,000 modular homes over the next five years. The housing association currently manages 33,000 affordable homes across the North West, Yorkshire and the Midlands,
The 38,000 sq metres of office space at the new Hinckley Power Station in Somerset will be the largest modular project in the UK and will house all the management and technical personnel required during the construction stage of the project. Part of the buildings will be converted after the construction cycle to remain as high quality offices for the permanent site.
UK-based design consultancy Arup and bridge specialist Mabey have recently announced that they have delivered the world's first modular, rapid-assembly glass fibre-reinforced polymer (GFRP) bridge.
The bridge was installed at a Site of Special Scientific Interest (SSSI) for Network Rail in Oxford. The bridge modules were light enough to be transported by an articulated lorry and then assembled on site and lifted from a distance.
Offsite pre fabrication succeeds as you need fewer experienced crafts people to supervise the less experienced. It has the double advantage that components can be constructed at a lower cost before being shipped to site for final installation.
It means that construction workers can be recruited from other industries, thus reducing the skills shortages, helping to increase productivity and reduce waste. The assembly line practices of prefabrication make offsite construction the perfect solution for contractors looking to reduce their dependence on skilled labour.
So if the pundits are right then modular offsite construction is set to boom – solving our acute skills shortage at the same time - bring it on.
By John Ridgeway
Follow me on Twitter @JohnRidgeway99
Additional Blogs
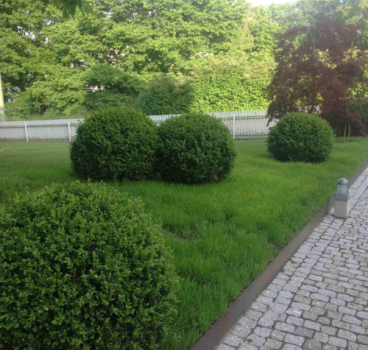
Why healthy soil is the hidden key to quality homes
Across countless new housing developments, a hidden problem is undermining quality and driving up customer complaints - and most housebuilders will never see it coming. The issue is not the homes...
Read moreThe fight for facades or why M&E must shape early design decisions
With sustainability and energy efficiency, not to mention decarbonisation, increasingly taking priority during building design, MEP engineers and architects are coming into conflict as part of an...
Read more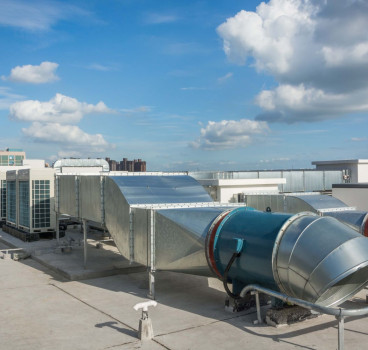
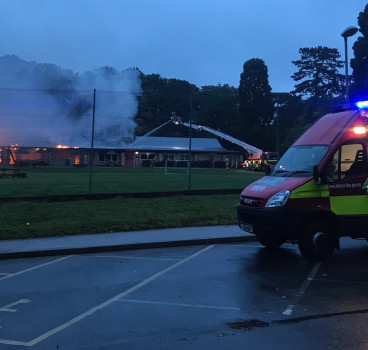
Back to school and the same old story on fire safety
We are about to start another school year and once again, we find ourselves having the same discussion about fire safety guidance for schools. The last attempt to revise Building Bulletin 100 (BB100)...
Read more