Why construction is failing to meet recycling targets
The aspirational vision of a circular economy in construction, promising reduced waste and lower embodied carbon, is collapsing under the weight of stubborn reality. Despite growing awareness and ambitious targets, genuine material reuse in the sector remains woefully low, consistently missing key aspirations. An examination of real-world barriers - including pervasive contamination, a glaring lack of appropriate standards and significant cost implications - reveals precisely why this circular ideal frequently encounters insurmountable practical hurdles, writes John Ridgeway.
The construction industry's entrenched "take-make-dispose" model is inherently unsustainable and financially inefficient. It consumes vast quantities of virgin aggregates, timber and metals, simultaneously generating enormous volumes of waste - much of which ends up in landfill, incurring significant disposal costs. The environmental footprint of extracting, processing and transporting new materials is substantial, contributing heavily to project embodied carbon.
In stark contrast, a truly circular approach seeks to drastically minimise resource input and waste output. This is achieved by designing out waste and pollution, keeping products and materials in use for as long as possible and regenerating natural systems. Material reuse, distinct from recycling (which involves energy-intensive reprocessing), represents the purest form of circularity where materials like bricks, steel beams, or timber are extracted from one building and directly redeployed in another with minimal alteration. The promised benefits are clear - reduced embodied carbon, decreased landfill burdens and the preservation of finite resources.
Despite this and notwithstanding numerous national and international policies championing circular economy principles with ambitious waste reduction targets, the operational reality of achieving widespread material reuse presents a formidable, often insurmountable, challenge for construction firms.
The problem of contamination
One of the most significant practical impediments to widespread material reuse is the pervasive issue of contamination, posing substantial financial and liability risks. Buildings are complex assemblies, with diverse materials often bonded, painted, or integrated in ways that make clean separation for reuse exceptionally difficult and costly.
Consider salvaged bricks. While intrinsically reusable, they are typically bound with mortar or caked with plaster and paint. Removing this residue to a standard suitable for direct redeployment is a highly labour-intensive and expensive process. The economics of cleaning thousands of individual bricks rarely justifies the cost against purchasing new, pre-cleaned materials, particularly given high labour rates in developed economies.
Beyond visible surface grime, unseen hazards present a critical deterrent. Older structures commonly contain asbestos, lead paint and various chemical treatments. Their presence necessitates specialist, hazardous material removal procedures that immediately render components unusable for reuse, even if the base material is structurally sound. The immense liability associated with inadvertently incorporating hazardous substances into a new building, or exposing workers to them during deconstruction, pushes contractors towards a default of demolition and landfill, overriding any potential reuse benefits. Without robust and reliable testing protocols for every batch of recovered materials, the risk profile is simply too high.
A second major hurdle undermining confidence in material reuse is the critical lack of standardised frameworks and reliable quality assurance for reclaimed components. New construction materials are manufactured to stringent specifications, undergoing rigorous testing and certification (e.g., CE marking or British Standards) that provide designers and contractors with absolute confidence in their performance, durability and safety. This vital assurance is largely absent for salvaged materials.
When specifying new steel beams, an engineer can demand a precise grade and performance. For a reclaimed beam, however, its exact grade may be unknown, its structural integrity potentially compromised by past stresses or corrosion and its fire resistance uncertain. Without a standardised method for assessing, grading and certifying the quality and performance of individual reclaimed components, specifiers are understandably reluctant to integrate them into new designs, especially for structural elements where failure carries catastrophic consequences.
This absence of a robust marketplace for certified reclaimed materials further compounds the problem. Unlike new materials, which benefit from established supply chains and clear pricing, sourcing reclaimed components often relies on ad-hoc, fragmented networks. There is no central registry detailing the availability, quantity, or certified quality of salvaged materials. This fragmentation, coupled with the lack of uniform testing protocols, makes it commercially difficult for designers to confidently specify reuse and for contractors to reliably procure suitable materials, acting as a significant barrier to mainstream adoption.
The cost-benefit imbalance
Despite the compelling environmental arguments, the adverse cost-benefit imbalance frequently acts as a decisive commercial factor against material reuse. While the raw material cost of reclaimed items might be lower or even zero, the associated labour, logistics and processing costs can rapidly render them uncompetitive.
Extracting materials for reuse demands careful deconstruction, a process far more time-consuming and labour-intensive than conventional demolition. While demolition rapidly smashes structures for lower-value recycling (e.g., crushing concrete for aggregate), deconstruction requires skilled labour to meticulously unbolt steelwork or carefully remove bricks. This higher labour cost for deconstruction often negates any saving from 'free' material.
Reclaimed materials typically require temporary storage, cleaning and sometimes re-processing before redeployment. This incurs significant costs for warehousing, specialised equipment and additional labour. The logistics of transporting salvaged materials from a demolition site to a storage facility, then to a new construction site, can also be more complex and expensive than the direct, streamlined delivery of new materials from a manufacturer.
Integrating reclaimed materials into a new design also demands flexibility from architects and engineers, who must often adapt their plans to available stock rather than specifying brand-new, precisely manufactured components. This can add complexity and cost to the design phase. Furthermore, the unpredictable lead times for sourcing specific reclaimed materials create critical uncertainty for project schedules, a significant commercial risk compared to ordering new materials with guaranteed delivery dates. The reliability and predictability of new material supply often outweigh the perceived benefits of reuse for project managers operating under tight deadlines.
Glimmers of progress
Despite these formidable barriers, concerted efforts and nascent developments are emerging to foster a more circular construction industry. Industry bodies and research institutions are actively developing standardised protocols for testing, grading and certifying reclaimed materials. The aim is to create a robust quality assurance framework that provides specifiers and contractors with the same level of confidence they hold in new materials, including methods for assessing structural integrity and the absence of hazardous contaminants.
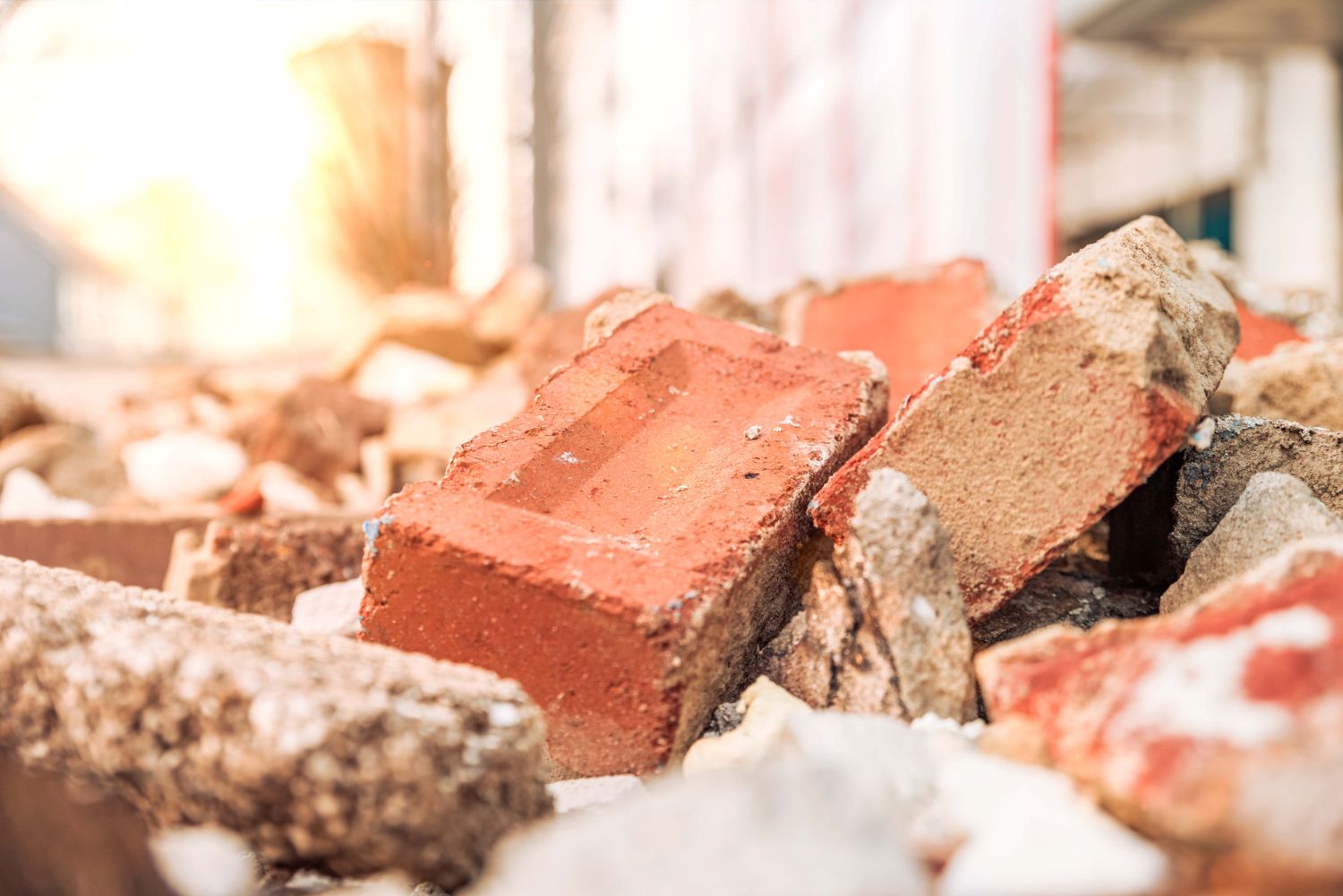
Furthermore, digital platforms and physical hubs are emerging to facilitate the exchange of reclaimed construction materials. These initiatives aim to increase visibility of available stock, streamline transactions and connect suppliers of salvaged materials with potential buyers, addressing the fragmented nature of the market and potentially reducing logistical costs.
A fundamental shift in architectural and structural design is also gaining traction. Design for Disassembly (DfD) considers a building's end-of-life at its inception, specifying materials and connections (e.g., bolted steel rather than welded) that facilitate easy and clean dismantling for material reuse. While primarily impacting new builds, it lays critical groundwork for a future where deconstruction for reuse becomes standard.
In addition, governments are exploring policy levers to encourage reuse, including tax incentives for reclaimed materials, stricter landfill taxes and mandates for a percentage of reused content in public procurement projects. Regulatory frameworks are also being investigated to streamline permits for buildings utilising reclaimed components.
Advances in robotics and artificial intelligence are also being explored to make deconstruction more efficient and less labour-intensive. Automated sorting technologies, robotic demolition tools and advanced scanning techniques for identifying hazardous materials could significantly reduce the costs and risks associated with material recovery.
We can see therefore, that the vision of a truly circular construction industry, where material reuse is commonplace, remains a significant commercial and environmental ambition. The current reality is challenged by deep-seated practical barriers such as pervasive contamination that inflates recovery costs, the absence of standardised testing and certification that undermines confidence and an unfavourable cost-benefit imbalance that discourages adoption compared to new materials. These factors combine to create a compelling disincentive for widespread material reuse, leading to ambitious targets remaining largely unmet.
However, the industry is not static. The development of new standards, the emergence of dedicated material marketplaces, the adoption of Design for Disassembly principles and the exploration of technological solutions for deconstruction represent vital steps forward. Overcoming the "circular construction myth" will require a concerted and sustained effort, demanding not just technological innovation, but also a fundamental shift in procurement practices, regulatory frameworks and collaborative industry mindsets. Only then can the ideal of material reuse transition from an elusive ambition to an achievable and widespread reality, genuinely reducing environmental impact and building a more sustainable future for the built environment.
Additional Blogs
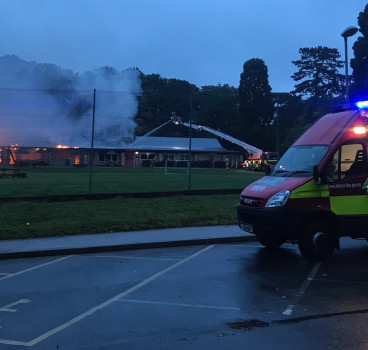
Back to school and the same old story on fire safety
We are about to start another school year and once again, we find ourselves having the same discussion about fire safety guidance for schools. The last attempt to revise Building Bulletin 100 (BB100)...
Read moreBEMS - the perfect fit for the UK’s retrofitting programme
While the Future Homes Standard (FHS) is exacerbating the need for property developers and house builders to incorporate energy efficient and sustainable technologies and materials into new build...
Read more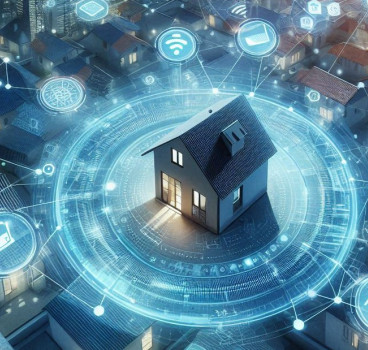
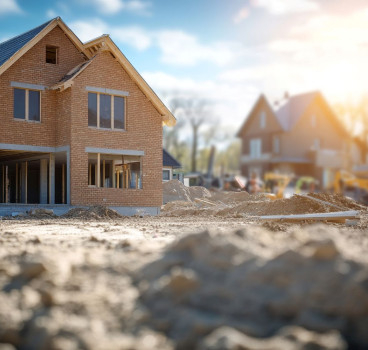
How Sustainable Drainage Systems (SuDS) are changing UK construction standards
For decades, drainage in UK construction has largely relied on traditional pipe systems designed to move rainwater quickly away from homes and roads into sewers. But with climate change bringing...
Read more