What Role Does Virtual Design and Construction (VDC) Play in Project Efficiency?
As a construction industry professional, you know the vital importance of efficiency. Preconstruction planning gives you a blueprint of tasks to follow, helping you stick to your budget, avoid delays and minimize design errors. VDC is one tool that can help you achieve detailed preplanning and efficient project completion.
Online forums abound with people criticizing the preconstruction process — but when combined with VDC and strong collaboration, it can be a game changer for meeting project deadlines. VDC is often particularly useful for large-scale projects with tight turnaround times.
What Is Virtual Design and Construction?
Construction project managers and their staff use VDC to digitally map out the construction process. Designers can build out 3D models so various players can identify potential problems and adjust before the building site ground is even broken.
You'll likely find architects and building engineers using VDC digital models to stay on schedule and within a budget. Contractors may also tap into the power of VDC to keep multiple tradespeople in the loop and combine all the moving parts of a building project.
VDC encompasses many types of digital reality to gather in-depth information for the project. In a study of over 750 designs by Stanford students, researchers found the majority of top-performing 3D models resulted from people using a digital pen to hand draw elements such as building information modeling (BIM).
There is still a place for architects and designers to add their creative mark to the process. Project managers often find that VDC offers the most value during the preconstruction phase.
How VDC Helps With the Preconstruction Process
Using VDC lets the team handle problems before they happen on the construction site. Tapping into the power of planning offers many key benefits, from big-picture workflow to the finest details.
1. Refine Design Accuracy
Digital models allow you to collaborate with all the stakeholders on a project and ensure designs meet client expectations. Computer models will also uncover any inconsistencies between different plans on the project. More accurate designs also lead to more accurate cost estimates, eliminating concern over budgeting limitations in the preconstruction phase.
For example, a 3D BIM model can identify possible problems with the building system. Perhaps the heating and cooling vent layout lies across a structural beam, and rerouting the system would prevent noise or potential issues down the line.
2. Fine-Tune Estimates
Another advantage of VDC in the preconstruction phase is keeping you within your budget. You'll know what quantity and types of materials you need to complete the project and estimate costs more precisely.
The construction budget can impact how quickly a project is completed or if it is finished at all. Around 70% of a project's budget is for hard costs, such as the physical products used for construction. Around 30% goes to intangible services such as permits, marketing and interest on loans. Understanding the full scope of your project’s costs will ensure you’ve accounted for every expense before breaking ground.
3. Identify Risks
VDC also helps the team predict any potential risks and establish a plan to mitigate them. For example, building in a zone where winter temperatures are excruciating can limit the time crews can work outside. You might also consider how many tornadoes or hurricanes typically occur during the months you'll be building and have a plan for dealing with the unexpected.
Input as many scenarios as needed to come up with a Plan B, Plan C and so on. The more prepared you are, the less time you’ll lose, keeping you on target for project completion.
4. Optimize Workflows
Tapping into the power of virtual reality (VR) and BIM allows you to consider various timelines and sequences. Some elements must be completed first, such as the foundation, plumbing and electrical systems. You'll have to schedule drywall installation and completion after the building's basic systems are in place.
However, you can adapt other situations if you know what can happen out of order. Can you install the outside brick wall while waiting for the drywaller to arrive? VDC and related tools can help you understand which moving parts can happen simultaneously without people getting in one another’s way. You can use the BIM models multiple times to simulate different scheduling scenarios.
5. Check Compliance
Throughout construction, you’ll meet with building inspectors and comply with various regulations for your location. One handy trick is to grab the International Building Code model and use it in the initial preconstruction phases. However, it is also critical to cross-check local laws and ensure all the materials and construction milestones will meet permit standards for your area.
Slow permit approval can delay projects significantly. Make sure you preplan for various phases and submit your requests as early as possible to stay on schedule.
All construction companies want a stellar reputation to help them gain repeat business and referrals. Sticking to legal standards and complying with regulations creates a positive brand image and makes it easier to work with permit officials in the future.
How VDC Impacts Project Efficiency
Although the biggest benefits of VDC occur during the preconstruction phase, the method also improves the efficiency of a project's construction phase. Some of the most noticeable advantages include:
- Fewer changes during construction, keeping you on schedule.
- Predetermined building details, ensuring the finished project is high quality.
- Better communication between different crews and stakeholders.
- Reduced waste, leading to lower construction costs.
Although you'll spend a lot of time in the preconstruction phase, you can tap into the benefits of VDC at any point in the process. Remember to input your progress so teams can review the details and adjust as needed for materials, methods and scheduling.
On-site, crews can consult the BIM models and figure out the best measurements without having to stop and study complex blueprints repeatedly.
The Future of VDC
Ongoing advances in technology make VDC more valuable than ever. However, implementation hasn't kept pace, with some of the software being costly for smaller construction companies and contractors. Those working with the models must be trained in the software to gain full control of planning.
As the world increasingly marches toward computerized methods, expect more projects to include VDC. Tapping into the power of BIM models and preconstruction planning can put you ahead of the competition and ensure you meet customer expectations.
Additional Blogs
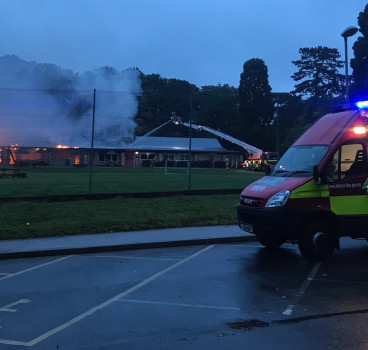
Back to school and the same old story on fire safety
We are about to start another school year and once again, we find ourselves having the same discussion about fire safety guidance for schools. The last attempt to revise Building Bulletin 100 (BB100)...
Read moreBEMS - the perfect fit for the UK’s retrofitting programme
While the Future Homes Standard (FHS) is exacerbating the need for property developers and house builders to incorporate energy efficient and sustainable technologies and materials into new build...
Read more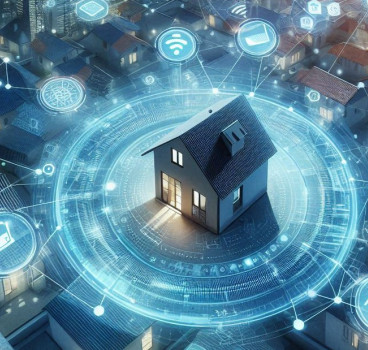
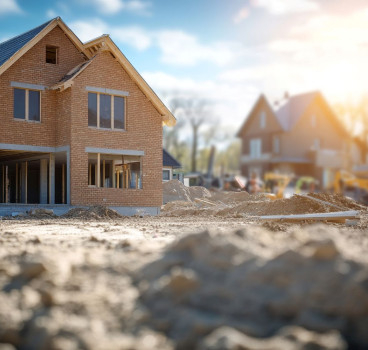
How Sustainable Drainage Systems (SuDS) are changing UK construction standards
For decades, drainage in UK construction has largely relied on traditional pipe systems designed to move rainwater quickly away from homes and roads into sewers. But with climate change bringing...
Read more