UK brick shortages and the rise of timber construction
The UK housing sector and the government's ambition to deliver 1.5 million new homes by 2029 is running headfirst into an uncomfortable reality - a shortage of bricks and skilled bricklayers. This bottleneck is not just a temporary glitch, it represents deeper structural issues that could redefine how homes are built in Britain for generations to come. Increasingly, developers are moving toward timber frame construction as a pragmatic solution, but is this a positive change, a necessary compromise, or a risky gamble, writes John Ridgeway?
For decades, the UK has underinvested in domestic brick manufacturing. Many brickworks closed during the late 20th century, particularly after the economic downturns of the 1980s and 2008. Today, brick production capacity is limited, supporting the construction of only around 250,000 homes per year, far short of government targets.
The shortage of skilled bricklayers is just as acute. A generation of tradespeople left the industry during the 2008 financial crisis and were not replaced in sufficient numbers. Efforts to revive apprenticeships and training programmes have been slow to yield results, exacerbating labour shortfalls.
Brexit also introduced new friction into material supply chains. While brick imports from Europe could once fill the gap, customs delays, tariffs and logistical uncertainties have made overseas sourcing less attractive and more expensive.
COVID-19 shutdowns further created a backlog of projects, leading to a surge in demand for materials and labour as the economy reopened. Brick manufacturers, already operating close to capacity, could not ramp up production fast enough.
Tougher environmental standards and the move towards more sustainable building practices have also increased pressure. Traditional clay bricks are energy-intensive to produce, clashing with broader decarbonisation goals.
The rise of timber frame
In response to these challenges, many developers are now opting more towards timber frame construction and it is easy to see the reasons why. Timber frames can be pre-fabricated and assembled rapidly onsite, cutting build times by 20-30% compared to traditional masonry construction. Timber frame homes also offer superior insulation properties, making them more energy efficient and aligned with net-zero carbon targets.
If sourced responsibly, timber is a renewable material with a significantly lower embodied carbon footprint than bricks or concrete. However, the biggest advantage is that timber frame construction requires less reliance on bricklayers. This move is already visible. In Scotland, where timber frame construction accounts for around 85% of new homes, compared to about 25% in England, but this is rising steadily south of the border as well.
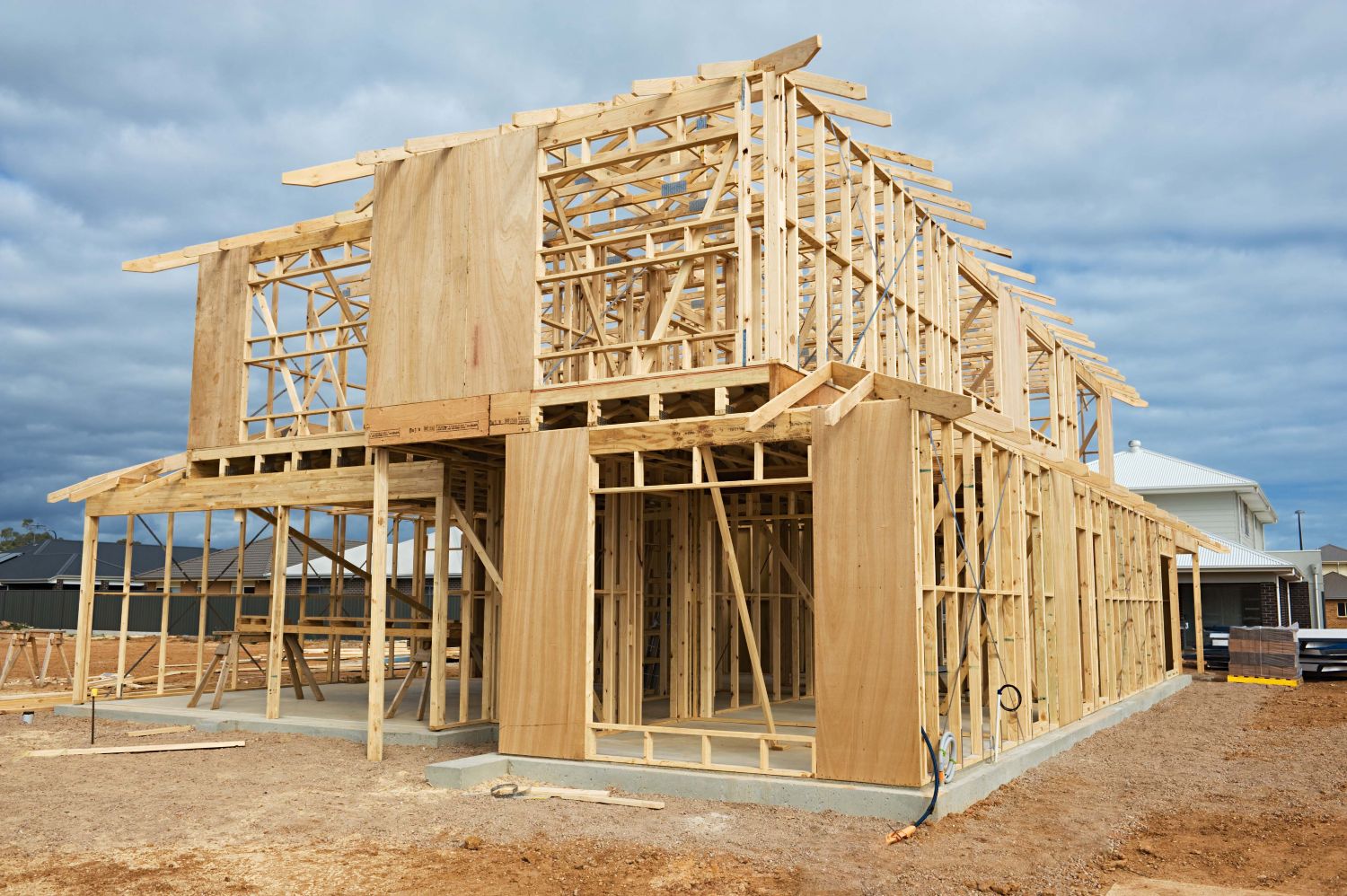
Despite the advantages, the widespread adoption of timber frame building is not without risks or controversy. High-profile fires, such as Grenfell Tower, have made fire safety a top priority. While properly designed timber buildings do meet fire regulations, public perception and insurance premiums, do not always reflect this.
Traditionalists also argue that brick-built homes better match the UK's architectural expectations. Some fear that rapid timber-based development could lead to uniform, uninspiring housing stock.
All this means that the UK government faces a delicate balancing act. One obvious solution is to invest heavily in expanding domestic brick production. New kilns, improved manufacturing technologies and incentives for brickworks could increase capacity, but these measures would take years to deliver and may not align with environmental goals.
A nationwide push to train a new generation of bricklayers could also help ease labour shortages, but again, results would take time. Training, qualification and gaining on-the-job experience can take several years, so it would seem that timber is only viable alternative, or are there other options?
Modern methods of construction
Timber frame building is just one aspect of the broader MMC movement, which includes modular homes, panelised systems and 3D printing. The government could provide grants, tax breaks, or regulatory support to accelerate adoption of these technologies.
As well as bricks and timber, other materials such as hempcrete, cross-laminated timber (CLT), and low-carbon concrete are gaining traction. A diversified material strategy could reduce reliance on any one approach.
However, for the moment, the move toward timber frame construction offers both opportunities and challenges for the construction industry. On the positive side it forces the industry to innovate and adopt quicker, greener construction methods. It aligns well with national net-zero carbon goals and has the potential to improve build quality through offsite manufacturing to reduce overall costs.
On the negative side there is the potential for early failures if quality control, maintenance and public trust issues are not carefully managed. The declining emphasis on masonry could also erode centuries of craftsmanship and architectural tradition and in time some suppliers and smaller contractors may struggle to adapt to the new landscape.
Ultimately, whether this is a positive change depends largely on what happens next. A thoughtful, standards-driven rollout of timber and other modern methods could make the UK housing sector more resilient, sustainable and fit for future challenges. A rushed, poorly regulated transition, on the other hand, could trigger costly problems down the line.
The brick shortage is a wake-up call for the UK construction sector. It highlights the risks of relying too heavily on traditional materials and skillsets without sufficient investment in future-proof alternatives.
As a result, timber frame construction is emerging not just as a stopgap solution, but as a long-term opportunity to rethink how Britain builds. The government, developers and insurers must work collaboratively to ensure that this shift results in high-quality, safe and beautiful homes that meet the needs of future generations.
The transition will not be easy. It will require retraining workers, retooling factories, rewriting regulations and reshaping public perceptions. But if done right, this could mark the start of a more dynamic, sustainable and innovative era in UK housebuilding.
Additional Blogs
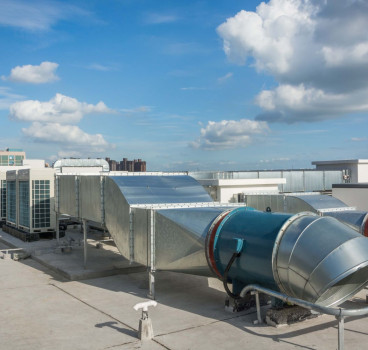
The fight for facades or why M&E must shape early design decisions
With sustainability and energy efficiency, not to mention decarbonisation, increasingly taking priority during building design, MEP engineers and architects are coming into conflict as part of an...
Read moreBack to school and the same old story on fire safety
We are about to start another school year and once again, we find ourselves having the same discussion about fire safety guidance for schools. The last attempt to revise Building Bulletin 100 (BB100)...
Read more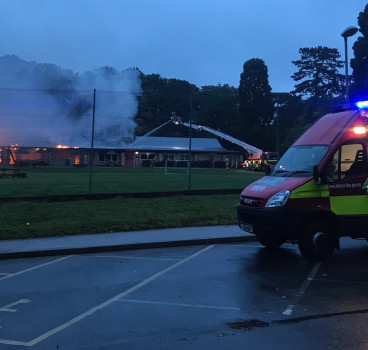
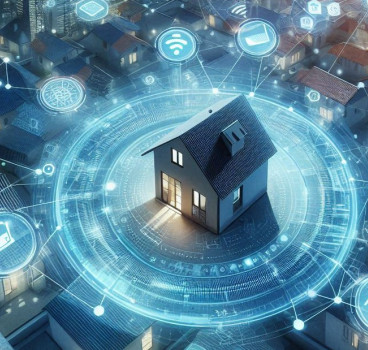
BEMS - the perfect fit for the UK’s retrofitting programme
While the Future Homes Standard (FHS) is exacerbating the need for property developers and house builders to incorporate energy efficient and sustainable technologies and materials into new build...
Read more