The real cost of “That’s How We’ve Always Done It” thinking in construction
It is a classic construction industry phrase and it goes something like this - “That’s how we’ve always done it” and it echoes through boardrooms and job sites across the world. However, while tradition holds value, clinging to outdated methods can hinder progress, efficiency and profitability – and it’s holding us all back, writes John Ridgeway.
As a result, productivity in construction has remained stubbornly low compared to other sectors. While industries like manufacturing, retail and agriculture have embraced automation, digital workflows and data-driven practices to boost efficiency, construction has been far slower to modernise. And this slow adoption is costing the industry dearly.
As long ago as 2017, McKinsey & Company reported that global labour productivity in construction had grown by just 1% annually over the previous 20 years. In contrast, the overall world economy grew at 2.8% and manufacturing grew at an even faster pace. If construction productivity were to catch up with the overall economy, it would then have to increase the industry's global value by $1.6 trillion annually. It is now 2025 and not much has changed.
One of the reasons, is that construction is highly fragmented. Small and medium enterprises (SMEs) dominate the sector and many lack the capital or motivation to invest in new tools or processes. With little incentive to innovate, many firms default to the status quo.
Unlike manufacturing, which benefits from standardised, repeatable processes, every construction project is unique. That makes it harder to apply one-size-fits-all innovations unless a company builds a culture of continuous improvement.
There is also a deeply ingrained mentality of "we’ve always done it this way." This conservatism can be a result of risk-aversion, generational gaps or even a lack of awareness about how impactful new technologies can be.
Inefficiencies mean that many projects run over schedule. The World Economic Forum estimates that 98% of large construction projects suffer cost overruns or delays. This means that labour costs rise when more time is needed to complete work that could be streamlined through automation, modular building, or digital design.
In addition, inaccurate drawings, poor communication and lack of coordination often result in mistakes that need to be fixed on-site. According to PlanGrid and FMI, rework alone costs the U.S. construction industry over $177 billion annually. This helps to ensure that the average profit margin in construction is often below 5% and poor productivity directly cuts into these already thin margins. Firms that fail to evolve risk being priced out by more agile competitors.
What can boost productivity?
In short, it is all about adopting many of the tools that have existed for some time. Building Information Modelling (BIM). enhances design accuracy and coordination between teams. Tools like Procore, PlanGrid, and Fieldwire streamline communication and documentation. Drones and Laser Scanning for site surveying and progress tracking, can also be adopted.
Prefabrication and modular construction allow for work to be done offsite in controlled environments, reducing weather-related delays and improving quality control. Lean construction principles borrowed from manufacturing, help focus on eliminating waste, optimising workflows and improving team collaboration.
One of Europe’s largest infrastructure projects, Crossrail (also known as the Elizabeth Line), used advanced digital modelling, prefabrication and real-time project monitoring. The use of digital twins and BIM allowed better coordination of the complex tunnelling and station construction. Despite some delays due to political and scope changes, the use of technology kept critical components on track and minimised costly rework. This stands as a solid example of how even massive public projects can benefit from improved productivity if there’s a will to innovate.
A global perspective
Looking at the situation globally, it is obvious that some regions are further ahead than others. Scandinavia and Singapore have embraced digital construction at scale, driven by supportive policies and public sector leadership. In South Korea, government mandates around BIM have accelerated its widespread use. China leads in prefabrication and high-rise modular construction, showcasing how productivity boosts can also align with environmental goals.
That phrase again - “That’s how we’ve always done it” is not just a mindset problem, it’s a productivity killer. Construction firms that resist change are missing out on profits, risking client satisfaction and jeopardising their long-term viability. To remain competitive, the industry must embrace innovation, process improvement and a new cultural outlook. The tools are already available - what’s needed now is the courage to change.
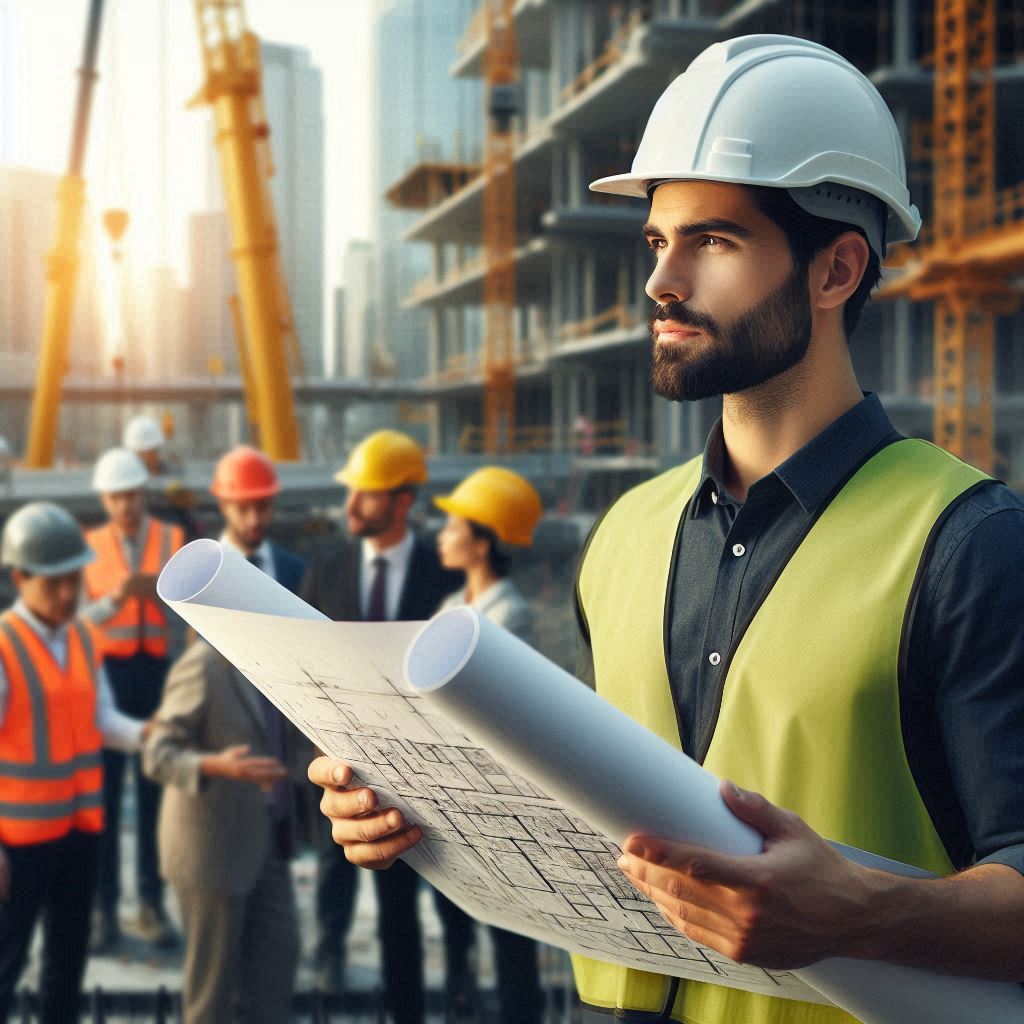
As already discussed, traditional methods, while familiar, can lead to inefficiencies. A study by the Construction Industry Institute found that projects using outdated practices experienced a 20% increase in schedule delays and a 15% increase in budget overruns compared to those implementing modern project management techniques.
Adhering to conventional practices can also compromise worker safety. The Occupational Safety and Health Administration (OSHA) reports that the construction industry accounts for one in five worker deaths annually in the U.S. Innovative safety technologies, such as wearable devices and real-time monitoring systems, have been shown to reduce incidents, yet their adoption remains limited due to resistance to change.
In a global market, construction firms must innovate to remain competitive. Companies that adopt new technologies and methodologies can offer clients faster, more cost-effective solutions, setting themselves apart from competitors who resist change.
Younger professionals entering the construction industry often seek employers who embrace innovation. Firms that invest in modern tools and foster a culture of continuous improvement are more likely to attract and retain top talent.
Modern construction practices, such as sustainable materials and energy-efficient designs, are also essential in addressing environmental concerns. Embracing these practices not only benefits the planet but also meets the growing demand for green construction solutions.
Strategies for change
Change must start at the top. Leaders should champion innovation, allocate resources for training and set clear expectations for embracing new methods. Providing ongoing training helps employees feel confident in adopting new technologies and processes. Workshops, seminars and hands-on experiences can facilitate smoother transitions.
Implementing small-scale pilot projects can allow firms to test new approaches, gather data, and make informed decisions before full-scale adoption. Encouraging feedback and open dialogue helps address concerns and fosters a culture of collaboration. Employees are more likely to embrace change when they feel heard and involved in the process.
The construction industry's reliance on the mantra “That’s how we’ve always done it” can no longer be justified in an era that demands efficiency, innovation and adaptability. By recognising the tangible costs of resistance and actively pursuing change, construction firms can position themselves for long-term success and resilience in a dynamic market – but will they?
Additional Blogs
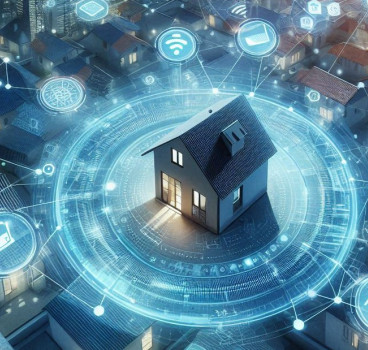
BEMS - the perfect fit for the UK’s retrofitting programme
While the Future Homes Standard (FHS) is exacerbating the need for property developers and house builders to incorporate energy efficient and sustainable technologies and materials into new build...
Read moreHow Sustainable Drainage Systems (SuDS) are changing UK construction standards
For decades, drainage in UK construction has largely relied on traditional pipe systems designed to move rainwater quickly away from homes and roads into sewers. But with climate change bringing...
Read more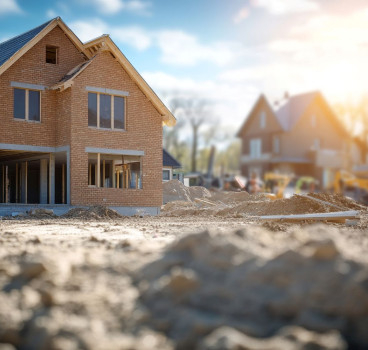
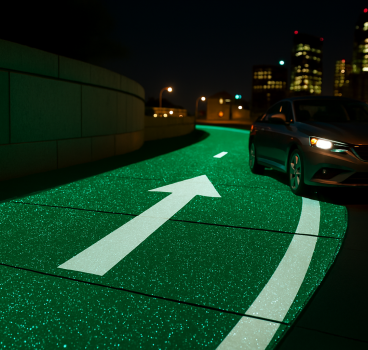
Why glow-in-the-dark concrete is a material for the future
Concrete is the backbone of modern civilisation and is one of the most widely used man-made materials on Earth, but for all its strength and versatility, concrete has never been thought of as...
Read more