Is material innovation outpacing building regulations?
The construction sector is experiencing a rapid evolution driven by advanced materials, yet regulatory frameworks are struggling to keep pace. New products, designed for enhanced performance, are quickly integrating into building designs and site operations. However, while this is accelerating material innovation, is also creating a significant challenge - with many sophisticated, lesser-known construction materials now operating in a regulatory grey area, writes John Ridgeway.
From advanced composites to complex chemical additives and intelligent coatings, these innovations often bypass traditional building regs and product standards. As a result, this oversight creates potential risks for long-term building performance, environmental impact and public safety. A more proactive and agile regulatory response is now critically needed to address this widening gap.
For decades, construction relied on a relatively stable choice of primary materials such as concrete, steel, timber and masonry. Regulations evolved to encompass their known properties, failure modes and safety implications. However, the last two decades have witnessed an explosion of material innovation, driven by demands for increased efficiency, sustainability, durability and novel functionality.
These materials, such as fibre-reinforced polymers (FRPs), combine two or more distinct materials to achieve superior properties. They are lightweight, possess high strength-to-weight ratios and exhibit excellent corrosion resistance, making them attractive for structural elements, bridge decks, facade panels and even internal fit-outs. While some composite applications, particularly in highly regulated sectors like aerospace, have stringent standards, their widespread and varied use in general construction often outpaces specific regulatory guidance.
Questions surrounding their long-term performance under various environmental stresses, fire resistance in different forms and end-of-life disposal or recyclability remain less comprehensively addressed by existing building codes. Their bespoke nature, often tailored for specific projects, makes broad classification and regulation challenging.
Specialised additives for traditional materials
We are also seeing more chemical additives, which are now routinely incorporated into traditional materials like concrete, mortar and renders. These can include superplasticisers to improve workability, air-entraining agents for frost resistance, accelerators for faster setting times and various polymers for enhanced durability or adhesion. While some well-established additives have long been part of industry practice, the constant development of new, often proprietary, formulations means that their long-term interactions, potential for unforeseen chemical reactions, or environmental implications (e.g., leaching of compounds into groundwater) may not be fully understood or adequately regulated. The cumulative effect of multiple additives within a single construction element presents a complex challenge for performance prediction and safety assessment.
Furthermore, intelligent coatings are emerging that offer active functionalities, such as self-healing properties that repair minor cracks, temperature-regulating capabilities that reduce energy consumption, antimicrobial surfaces for healthcare environments and even coatings that can monitor structural integrity and report data. These cutting-edge materials operate on principles far removed from conventional paints or renders.
Regulating such materials requires understanding not just their chemical composition and adhesion, but also their functional performance over time, their longevity of "smart" properties and their potential interactions with other building elements or environmental factors. Current regulations, largely focused on fire spread and basic durability for coatings, are ill-equipped to assess these multi-functional products.
All this means that several interconnected factors can contribute to why these innovative materials are often flying under the radar of comprehensive regulation. The development of new materials and their market introduction typically far outstrips the pace at which regulatory bodies can conduct thorough research, develop appropriate testing methodologies and enshrine new standards into law. Drafting and implementing new regulations is a protracted process, often taking years from initial discussion to legal enactment. By the time a standard is established for one generation of material, several new iterations or entirely new products may already be in widespread use.
Performance-based v prescriptive regulations
Many traditional building regulations are prescriptive, dictating precisely which materials can be used for specific applications or requiring adherence to known material standards (e.g., British Standards for steel or concrete). However, modern materials often exhibit novel properties that do not fit neatly into existing prescriptive categories. A move towards purely performance-based regulations, while more flexible, requires robust and universally accepted testing regimes that can accurately assess long-term behaviour, a challenge for entirely new material classes. The current regulatory landscape often operates in a hybrid model, which struggles to accommodate radical material departures.
The highly complex chemical and physical properties of many new materials, particularly when used in combination, make their assessment difficult. For instance, the long-term interaction between a novel additive in concrete and a new type of reinforcing fibre might not be fully understood through standard individual material tests. The interconnectedness of modern building systems means a failure in one seemingly minor component could have cascading effects, yet regulations often assess materials in isolation.
In addition, manufacturers of innovative materials often consider their formulations and performance data as proprietary intellectual property. While some data is provided for certification, the full breadth of research and testing may not be publicly accessible or subject to independent third-party scrutiny. This lack of transparent, comprehensive data makes it challenging for regulators to conduct thorough, unbiased assessments and to develop robust standards. Independent long-term performance studies are also scarce for many recently developed materials.
The globalised nature of construction material supply chains complicates regulation further. Materials are sourced from various countries, each with differing national standards and enforcement mechanisms. While frameworks like the UKCA marking (and continued acceptance of CE marking) aim to ensure product conformity for market entry, these primarily focus on facilitating trade, not necessarily guaranteeing specific safety performance for every novel application within a building. The onus is often placed on the specifier or contractor to verify suitability, but without clear, universal regulatory backing, this can be an onerous and risky task.
The most critical concern is public safety. Without rigorous testing and clear regulatory guidelines for fire performance, structural integrity under load, long-term durability and resistance to environmental degradation, there is a tangible risk of unforeseen failures. A coating that loses its fire-retardant properties prematurely, a composite panel that degrades unexpectedly in adverse weather, or an additive that weakens concrete over time could have catastrophic consequences, particularly in high-rise or high-occupancy buildings.
Unpredictable performance and durability
Building owners and occupants rely on structures to perform reliably over their intended lifespan. If the long-term behaviour of a new material is not fully understood or properly regulated, buildings may not achieve their expected durability. This can lead to premature degradation, costly repairs, increased maintenance requirements and a reduced asset life, impacting economic viability and sustainability goals. The "unknown unknowns" of material performance poses a significant commercial risk.
Furthermore, while many new materials are developed with sustainability in mind, their full environmental footprint, from production to disposal, may not be adequately assessed or regulated. For instance, composite materials, while lightweight, can be challenging to recycle at the end of their life, potentially leading to landfill accumulation. Chemical additives might have unforeseen environmental consequences if they leach into soil or water. Without comprehensive lifecycle assessments and regulatory oversight, the purported environmental benefits might not fully materialise, or new environmental problems could emerge.
The use of unregulated or under-regulated materials also introduces considerable commercial risk. If a material fails, the legal liability can be complex and expensive, potentially leading to costly disputes, litigation and reputational damage for all parties involved - manufacturers, specifiers, contractors and building owners.
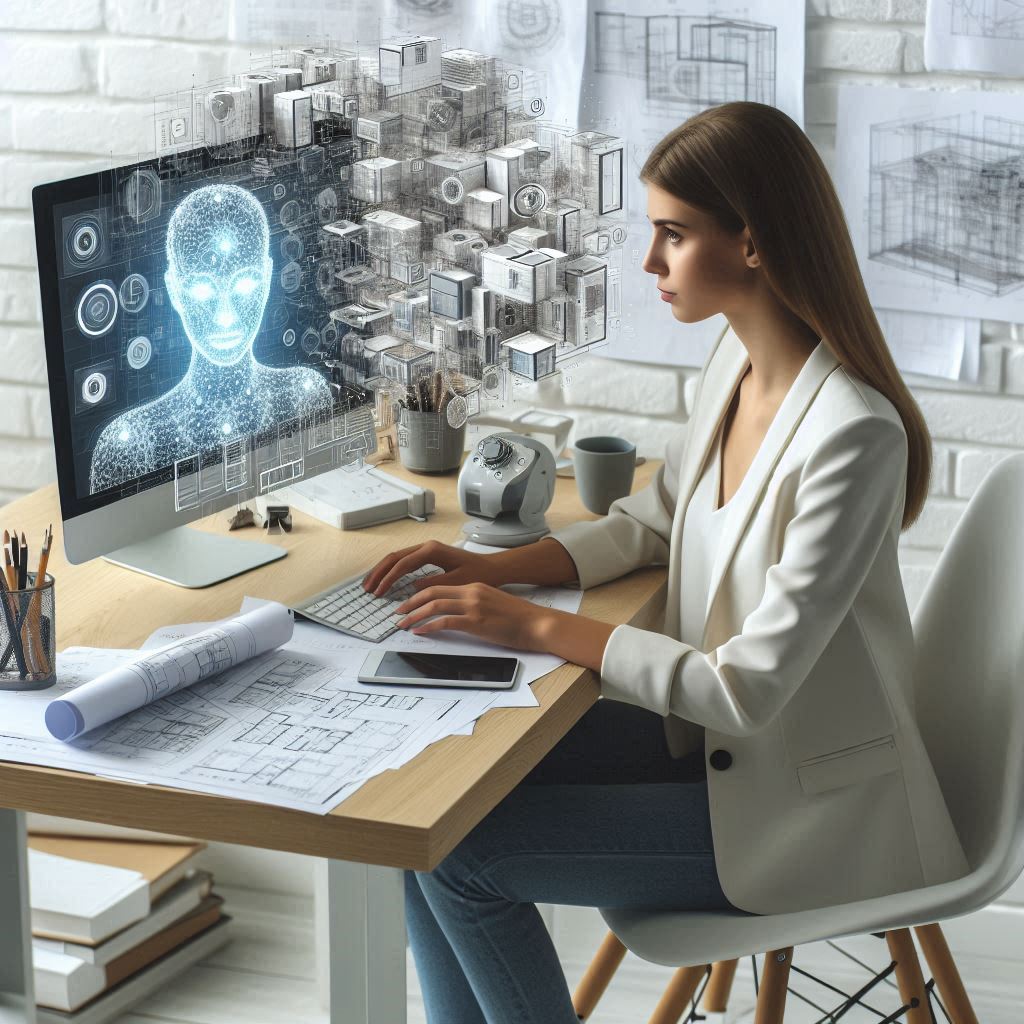
All this means that addressing the challenge of regulating emerging construction materials requires a fundamental shift in approach for governing bodies and industry stakeholders. Regulatory bodies need to adopt more agile and responsive processes for developing new standards. This could involve creating fast-track approval routes for demonstrably safe innovations, establishing clearer performance-based criteria and moving away from overly prescriptive rules. Collaboration with research institutions and material scientists is crucial to quickly understand the properties of new products.
Investment in independent, advanced material testing and research facilities is also essential. These centres can undertake comprehensive, long-term studies on emerging materials, providing the robust, unbiased data necessary for informed regulation. Such facilities could also offer accredited testing services for manufacturers, ensuring transparency and reliability of performance claims.
Regulation should extend beyond immediate safety and structural integrity to encompass the full lifecycle environmental impact of materials. Mandating comprehensive lifecycle assessments (LCAs) for new materials, from raw material extraction to end-of-life disposal or recycling, would provide a more holistic view of their sustainability credentials and drive industry towards genuinely green solutions.
Manufacturers should be encouraged, and potentially required, to share more comprehensive, independently verified data on their material properties and performance. A central, accessible database of certified construction products, including detailed performance characteristics and testing results, would empower specifiers, contractors and regulators to make informed decisions.
Given the global nature of material supply, increased international collaboration on standards development and mutual recognition of testing protocols would further streamline the regulatory process and ensure a consistent level of safety and performance across borders. This would reduce complexity for manufacturers and enhance confidence for users.
We can see therefore, that the proliferation of advanced construction materials - from innovative composites and chemical additives to smart coatings - presents both immense opportunities and significant, often unaddressed, regulatory challenges. Many of these products are currently operating in a blind spot, lacking the comprehensive oversight commensurate with their widespread use and potential impact on safety, durability and environmental performance.
This regulatory void creates unacceptable risks for building occupants, owners and the broader industry. A proactive, agile and technologically informed regulatory approach is imperative. By investing in research, embracing data transparency, fostering collaboration, and accelerating standard development, the construction sector can ensure that innovation in materials science genuinely contributes to a safer, more sustainable and higher-performing built environment, rather than inadvertently introducing new, unquantified threats.
Additional Blogs
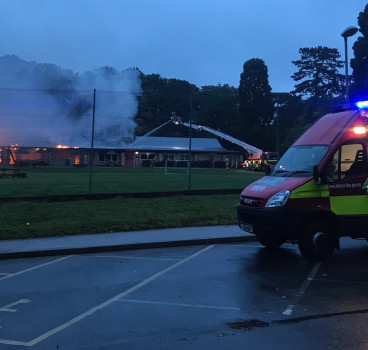
Back to school and the same old story on fire safety
We are about to start another school year and once again, we find ourselves having the same discussion about fire safety guidance for schools. The last attempt to revise Building Bulletin 100 (BB100)...
Read moreBEMS - the perfect fit for the UK’s retrofitting programme
While the Future Homes Standard (FHS) is exacerbating the need for property developers and house builders to incorporate energy efficient and sustainable technologies and materials into new build...
Read more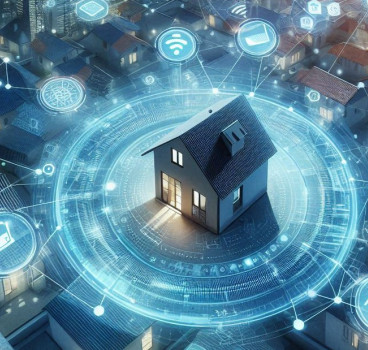
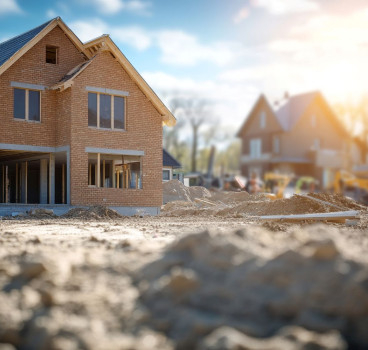
How Sustainable Drainage Systems (SuDS) are changing UK construction standards
For decades, drainage in UK construction has largely relied on traditional pipe systems designed to move rainwater quickly away from homes and roads into sewers. But with climate change bringing...
Read more