How slave labour in the supply chain affects ethical projects
There is a darker, often overlooked issue behind some of the materials we so proudly label as "eco-friendly." Ethical labour practices, specifically the risk of forced or slave labour within global supply chains now present a moral and reputational challenge that the industry can no longer afford to ignore. All building materials have a backstory, but too often, that story includes exploitative working conditions, unpaid wages and human rights abuses in far-flung corners of the world. As developers, contractors and specifiers, we are not just building structures - we are also shaping the legacy of how they were built. The question we must therefore ask is - "was it ethically sourced?" Because if your project turns a blind eye to forced labour, then no amount of carbon offsetting can make it truly responsible, writes John Ridgeway.
Modern slavery encompasses a range of exploitative practices, including forced labour, debt bondage, human trafficking and child labour. According to the International Labour Organisation (ILO), over 27 million people worldwide are estimated to be trapped in modern slavery. A significant portion of this number is linked to global supply chains, with the construction sector identified as a high-risk industry.
Materials such as steel, bricks, timber, stone and even solar panels have been linked to regions or industries where forced labour is rife. The issue is not confined to distant corners of the world. It can manifest closer to home, especially on sites that rely on unregulated labour or subcontractors with opaque hiring practices.
The construction industry relies on a vast network of international suppliers, often sourced based on cost and availability rather than traceability or ethical standards. Long and opaque supply chains make it easy for unethical practices to remain undiscovered, particularly in countries where worker protections are weak or poorly enforced.
Moreover, construction projects often face tight timelines and budgets. This pressure can drive developers and contractors to turn a blind eye to ethical considerations in favour of expediency and cost-saving. This culture of "just get it done" is precisely what allows unethical labour practices to thrive.
Who bears responsibility?
The responsibility for ensuring ethical labour practices does not fall on one group alone. Developers, contractors, specifiers and procurement teams all have a role to play. Developers set the tone from the outset. As project initiators, they wield significant influence over the supply chain. By embedding ethical sourcing requirements into project briefs, contracts and procurement frameworks, developers can create a culture of accountability from day one.
Ethical sourcing must be a non-negotiable principle rather than a "nice to have." Developers should prioritise suppliers with clear, transparent labour practices and robust supply chain management systems. They can also require third-party certifications and regular audits.
Main contractors and subcontractors are also in a unique position to either uphold or undermine ethical standards. While it is tempting to subcontract to the lowest bidder, doing so without due diligence opens the door to exploitation.
Contractors must therefore ensure that all tiers of their supply chain - right down to material sourcing - adhere to ethical practices. This means carrying out thorough vetting of suppliers, requesting documentation of labour conditions and being willing to terminate contracts if unethical behaviour is discovered.
Furthermore, on-site labour practices must be closely monitored. Recruitment processes should be transparent and workers should be protected from abuse, underpayment and unsafe conditions. In the UK and other regions, modern slavery legislation places legal obligations on companies to publish transparency statements and demonstrate due diligence.
Architects, engineers, and designers also have a crucial role to play. Specifiers influence which materials are selected for a project, often determining the regions and industries that benefit from procurement decisions.
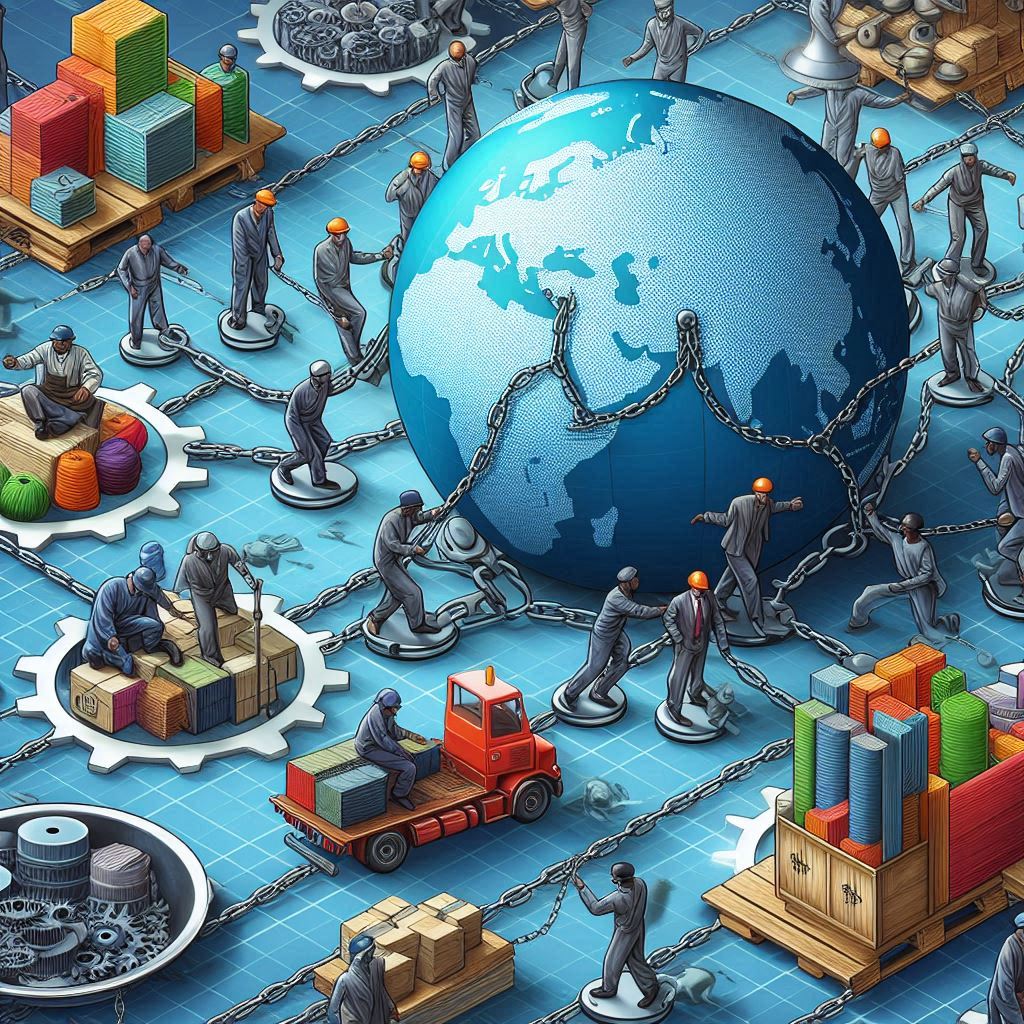
By choosing ethically sourced products, specifiers can reduce the demand for materials tainted by forced labour. This requires collaboration with suppliers who prioritise traceability and ethical standards, as well as a willingness to consider alternative materials or products that meet both performance and ethical criteria.
Specifiers can also influence industry standards by advocating for transparency and pushing for certifications such as FSC (Forest Stewardship Council) for timber or BES 6001 for responsibly sourced construction products.
What can be done?
Combatting modern slavery in construction is not easy, but it is possible. It requires systemic change, persistent vigilance and a commitment to ethical practices at every level. You should be aware, of where your supply chain may be vulnerable to unethical practices. High-risk countries, industries known for exploitation and opaque subcontracting structures should all be flagged. Use tools like the Global Slavery Index or country-specific risk assessments to guide decision-making.
Make ethical sourcing a contractual requirement. Include provisions that require suppliers to disclose their own supply chains and commit to fair labour practices. Contracts should also allow for audits and impose penalties for non-compliance. Work with suppliers who carry certifications that reflect ethical labour practices. While not perfect, certifications such as ISO 20400 (Sustainable Procurement) or SA8000 (Social Accountability) offer a benchmark for responsible sourcing.
However, do not assume that once a supplier has been vetted, the job is done. Regular audits - both internal and by third parties - are essential to ensure ongoing compliance. Audits should be unannounced and should include interviews with workers where possible.
Awareness is key. Developers, contractors and procurement officers must be trained to understand the signs of modern slavery and know what steps to take if issues are suspected. Ethical sourcing should be a core component of project management and procurement training. This is not a challenge to be tackled in isolation. Join industry initiatives, share best practices and collaborate with NGOs and certification bodies. By creating an ecosystem of accountability, the industry can collectively drive meaningful change.
The business case for ethical supply chains
In addition to the moral and legal obligations, there is a compelling business case for ethical sourcing. Clients, especially public sector and international customers, increasingly demand a demonstrable commitment to social responsibility. Ethical practices can be a differentiator in a crowded market, enhancing reputation and winning contracts. Moreover, unethical supply chains come with significant risks - legal liability, reputational damage, project delays and financial penalties. By prioritising ethical sourcing, companies protect their bottom line while doing the right thing.
The question of ethics in construction is not theoretical. It affects real people - men, women, and children forced to work in dangerous and degrading conditions to produce the materials we use every day. Turning a blind eye is no longer an option.
As professionals in the built environment, we have both the power and the responsibility to shape a more ethical industry. By questioning where our materials come from, demanding accountability and embedding ethical practices into every project, we can ensure that our buildings are not only functional and beautiful, but also just. So, the next time you specify a material, sign off on a supplier, or choose a contractor, ask yourself - is this project ethical? Because if we don’t ask - and act - then who will?
Additional Blogs
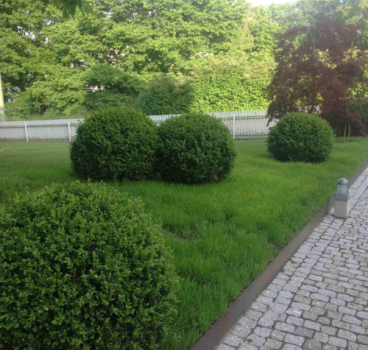
Why healthy soil is the hidden key to quality homes
Across countless new housing developments, a hidden problem is undermining quality and driving up customer complaints - and most housebuilders will never see it coming. The issue is not the homes...
Read moreThe fight for facades or why M&E must shape early design decisions
With sustainability and energy efficiency, not to mention decarbonisation, increasingly taking priority during building design, MEP engineers and architects are coming into conflict as part of an...
Read more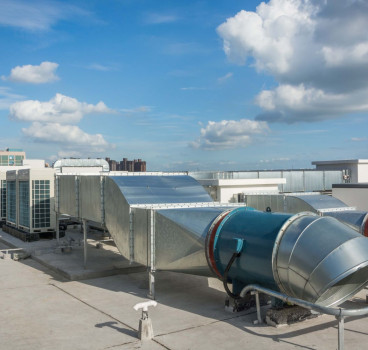
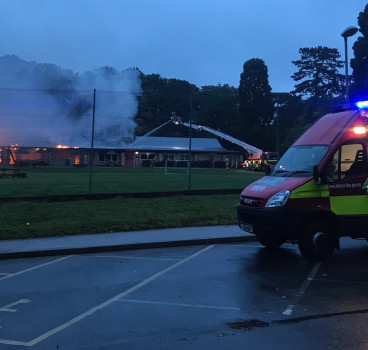
Back to school and the same old story on fire safety
We are about to start another school year and once again, we find ourselves having the same discussion about fire safety guidance for schools. The last attempt to revise Building Bulletin 100 (BB100)...
Read more