How AI and Robotics are powering the rise of ‘Dark Sites’ in construction
In the ever-evolving landscape of construction, a new trend is emerging - 'dark sites' - where autonomous machines and AI-driven systems operate around the clock, often without human supervision. These sites represent a significant move from traditional construction methods by using advanced technologies to enhance efficiency, safety and productivity, writes John Ridgeway.
The concept of 'dark sites' borrows from the manufacturing industry's 'lights-out' factories, where automation allows for continuous operation without human intervention. In construction, this translates to job sites where robots and AI systems perform tasks such as excavation, bricklaying, surveying and material handling during off-hours, maximising productivity and minimising downtime.
The journey toward fully autonomous construction - culminating in today’s emerging 'dark sites' - is not a sudden leap, but the result of decades of innovation, experimentation and technological integration. From the first hints of mechanised creativity in architecture to AI-driven robotics, each step forward has reshaped how we think about the building process.
The roots of automated construction can be traced back to the mid-20th century, when visionaries began exploring how technology could reshape the way we build. One of the earliest pioneers was Dante Bini, an Italian architect who, in the 1960s, introduced the Binishell - a revolutionary system that used inflated air pressure to form reinforced concrete domes. This method allowed for quick, cost-effective construction of durable structures and marked one of the first known instances where automation replaced traditional manual processes in building.
Binishells were deployed for schools, emergency shelters and even military installations. Though primitive by today’s standards, Bini’s work foreshadowed a world where machines would shape buildings with minimal human input.
Rise of robotics and digital control
As computing power improved in the late 20th century, industries began experimenting with robotic systems - though adoption in construction lagged behind due to the complexity and variability of job sites.
In the 1980s and 1990s, Japan emerged as a leader in construction robotics, driven by its own labour shortages and high demand for infrastructure. Companies like Shimizu Corporation and Obayashi developed prototype robotic arms and crane-mounted bots capable of tasks like concrete pouring and welding in high-rise buildings.
Meanwhile, academic institutions, such as ETH Zurich and MIT, began experimenting with digital fabrication techniques, including robotic arms and CNC machines tailored for architectural design. These experiments laid the foundation for robotic masonry, automated formwork and 3D printing in architecture.
In spite of these advances, most of these systems remained confined to laboratories or one-off pilot projects due to high costs, limited mobility and the unpredictable nature of outdoor construction sites.
The 2010s marked a tipping point. With rapid advances in sensors, machine vision, GPS, cloud computing and AI, construction technology firms began transforming theory into scalable solutions.
In 2016, Built Robotics became a trailblazer by introducing the Exosystem - a retrofit kit that turns traditional construction equipment like excavators and bulldozers into autonomous, GPS-guided machines. These machines could perform essential tasks like trenching and grading without human operators, guided by preloaded digital maps and real-time sensor feedback.
Built Robotics’ Exosystem brought autonomy to the rugged, unstructured environments of real-world construction sites - a key challenge that earlier robotic systems failed to overcome. These machines are now in use across solar farm installations and civil infrastructure projects, operating with minimal supervision.
Across the globe in Australia, Fastbrick Robotics (FBR) introduced the world to Hadrian X, a robotic bricklaying system capable of laying over 1,000 bricks per hour - each one placed with millimetre precision using a combination of laser guidance and CAD modelling.
Launched publicly in the late 2010s, Hadrian X fundamentally changed perceptions around construction automation by solving a real-world problem - chronic bricklayer shortages and inconsistent masonry work. Its real-world applications now extend to residential housing developments, where FBR has partnered with major builders to scale operations.
These two innovations signalled a shift from one-off prototypes to commercially viable autonomous systems, pushing the concept of 'dark sites' from future fiction into present-day pilot projects.
Digital twins, BIM, and the AI-driven ecosystem
Alongside physical robotics, the software side of construction has evolved in parallel. The rise of Building Information Modelling (BIM), digital twins and AI-driven site management platforms like Versatile or nPlan has made it possible to not only automate physical tasks, but also to simulate, plan and optimise entire workflows before a spade hits the ground.
These systems feed into autonomous machinery, providing real-time updates, progress tracking and predictive analytics. They allow machines to adjust their tasks dynamically based on actual site conditions - a critical step toward truly autonomous site management.
The late 2010s also saw rapid progress in 3D-printed buildings, with robotics playing a central role. Construction 3D printers use robotic arms or gantry systems to extrude concrete or other materials in precise, layered sequences.
Toward fully autonomous 'Dark Sites'
Today, the concept of 'dark sites' - fully or semi-autonomous construction zones that operate with minimal human oversight - is not only technically feasible, but increasingly commercially attractive.
Firms like Built Robotics, FBR, and newer entrants like Canvas (which automates drywall finishing) and HP SitePrint (which handles autonomous site layout) are paving the way for entire workflows to be managed by machines.
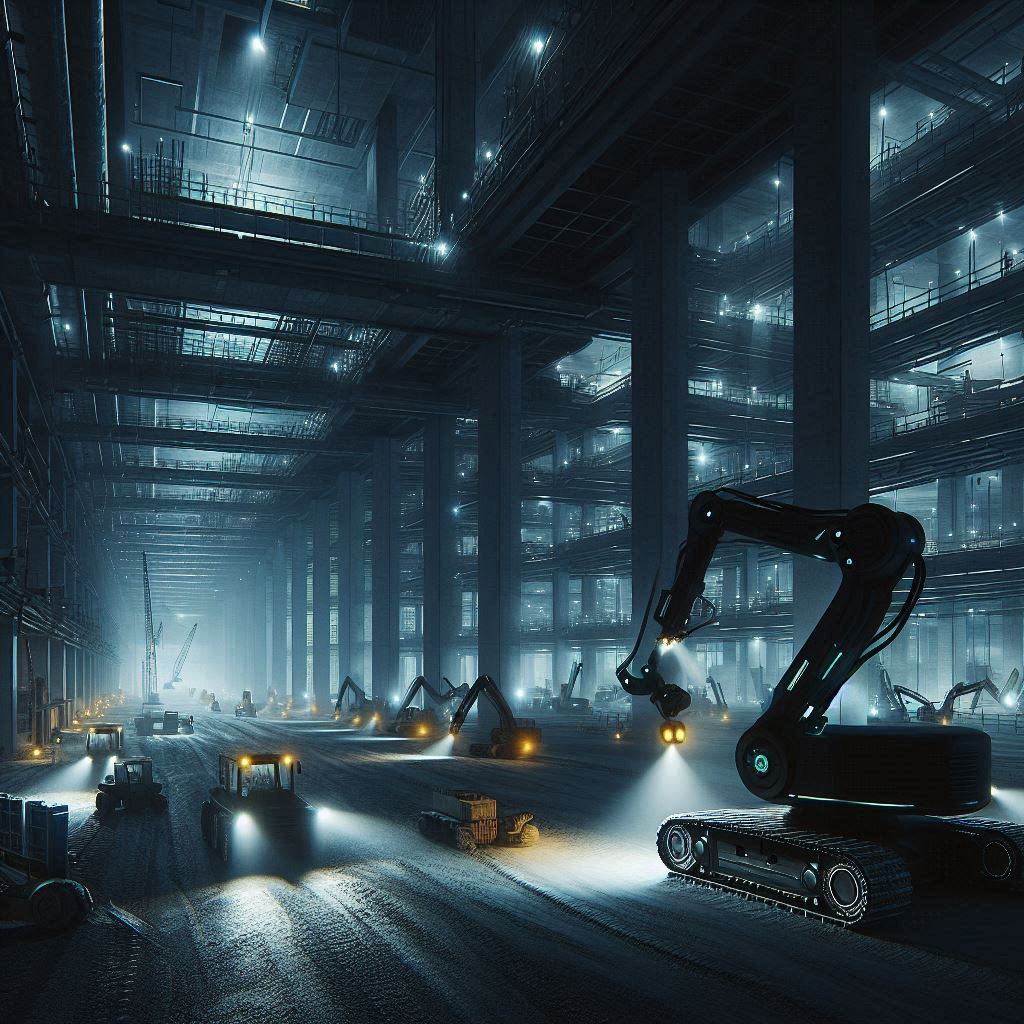
On some solar farms, remote wind installations, or industrial projects, entire site prep operations - grading, trenching, layout and concrete formwork - can now be carried out overnight and without lighting.
With ongoing advances in AI, robotics and digital integration, the future of autonomous construction is accelerating fast. Key developments on the horizon include swarm robotics, where multiple machines communicate and coordinate like a hive and self-healing materials, which reduce the need for human maintenance.
Autonomous quality assurance, using drones and AI to detect flaws in real time are working alongside human-machine collaboration, where onsite supervisors guide fleets of robots from tablets or VR interfaces.
Governments and regulators are also beginning to explore policy frameworks for machine-operated construction, indicating that this is no longer a fringe experiment, but a fundamental shift in how infrastructure will be built.
Benefits of 'Dark Sites'
This is because traditional construction sites are bound by human working hours, weather conditions and logistical constraints. 'Dark sites', however, can operate 24/7, unaffected by fatigue, shift limits, or even some environmental conditions like darkness or light rain.
Autonomous machines - such as robotic excavators or bricklaying bots - can work through the night, completing critical groundwork or structure assembly without pause. This level of continuous operation means that what once took weeks can now be completed in a matter of days, accelerating project timelines and potentially cutting labour costs by up to 40%.
In remote areas of the U.S., solar farm developers have already begun using autonomous earthmovers from Built Robotics to prepare terrain overnight, ensuring that human crews can begin installation work first thing in the morning - doubling productivity across the board.
And because construction remains one of the most dangerous industries globally, with workers facing risks such as falls, equipment accidents and exposure to hazardous materials. 'Dark sites' drastically reduce human presence in these high-risk environments by delegating dangerous tasks to machines.
Robots don’t get distracted, tired, or overwhelmed by environmental hazards. For example, demolition robots can handle unstable structures without putting human lives at risk. AI-guided machinery can assess structural integrity and operate in confined or contaminated spaces - areas where sending human workers would be irresponsible or even unlawful under safety regulations.
In Japan, for example, demolition robots were deployed to safely dismantle parts of the Fukushima nuclear site - an environment too dangerous for humans due to radiation. This concept is now being adapted for civilian construction to mitigate risks on unsafe or aging buildings.
Robots don’t rely on “gut feel.” They follow digital blueprints with millimetre-level accuracy, ensuring consistent output across large-scale projects. This reduces human error, limits material waste and enhances structural integrity.
Autonomous construction systems also provide real-time quality control. For example, robotic arms used in 3D concrete printing can monitor pressure, material viscosity and temperature as they build - adjusting parameters instantly to ensure smooth surfaces and even layering.
This has happened in Dubai, where a government-backed 3D-printed office building was erected with robotic precision, showcasing not just speed, but immaculate architectural accuracy. The end product was 30–40% more material-efficient than traditional methods and finished in just weeks.
AI-backed robotics also enable consistent finishes, whether it's applying plaster, drilling holes, or installing tiles. This uniformity leads to fewer callbacks, less rework and higher client satisfaction.
Another and often overlooked, but critical benefit of 'dark sites' is their environmental sustainability. Automated systems optimise the use of materials and energy, reducing waste and emissions.
Robotic systems can be programmed to use just-in-time material handling, minimising storage needs and avoiding spoilage. Combined with AI-driven logistics and scheduling software, these systems also optimise deliveries to avoid idling trucks, congestion and excessive fuel use.
Data-driven insights and predictive maintenance
An additional bonus is that ‘Dark sites’ generate vast amounts of data - from machine performance to construction progress and material consumption. This data is invaluable when fed into AI systems for predictive maintenance, project analytics and budget forecasting.
For instance, AI can detect patterns that indicate equipment wear, allowing maintenance teams to intervene before failures occur - reducing downtime and costly repairs. Similarly, by tracking the rate at which tasks are completed, project managers can fine-tune schedules and resource allocation for future builds.
However, implementing autonomous systems requires significant upfront investment in technology and training, but the long-term benefits often outweigh the initial costs. Furthermore, while AI and robotics have advanced, they still face challenges in adapting to dynamic and unpredictable environments common in construction sites. The use of autonomous machines also raises questions about job displacement and regulatory compliance. Clear guidelines and policies are needed to address these concerns.
That said, the emergence of 'dark sites' marks a significant milestone in the construction industry's evolution. By embracing AI and robotics, the industry can overcome longstanding challenges, improve efficiency and pave the way for a safer, more productive future.
The evolution of autonomous construction spans nearly 60 years - from Dante Bini’s inflatable concrete domes to today's AI-guided diggers and bricklaying robots. What began as speculative architecture has matured into a multi-billion-pound frontier.
These advances have not just made construction faster and cheaper - they’ve redefined the limits of what’s possible, enabling safer, smarter and more sustainable environments. With the first dark sites now in operation, the future of construction is not just autonomous - it’s already under way.
Additional Blogs
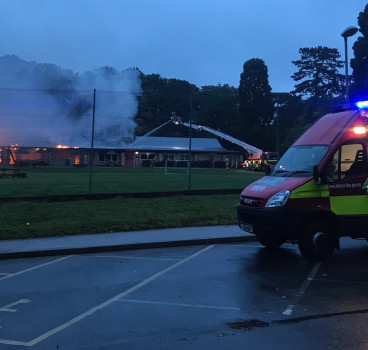
Back to school and the same old story on fire safety
We are about to start another school year and once again, we find ourselves having the same discussion about fire safety guidance for schools. The last attempt to revise Building Bulletin 100 (BB100)...
Read moreBEMS - the perfect fit for the UK’s retrofitting programme
While the Future Homes Standard (FHS) is exacerbating the need for property developers and house builders to incorporate energy efficient and sustainable technologies and materials into new build...
Read more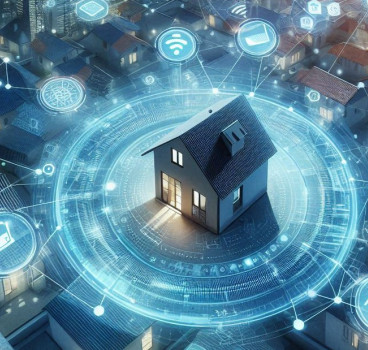
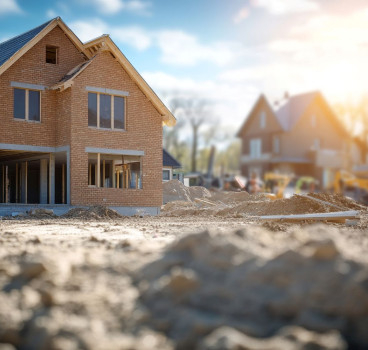
How Sustainable Drainage Systems (SuDS) are changing UK construction standards
For decades, drainage in UK construction has largely relied on traditional pipe systems designed to move rainwater quickly away from homes and roads into sewers. But with climate change bringing...
Read more