Flooring that offers a picture of health
Human health and wellness is at the forefront of building design with the emergence of the WELL Building Standard® (WELL), the first standard of its kind which rates a building's impact on occupants and gives a single ‘wellness' rating for buildings. But what are the challenges for the specifier and contractor to meet this standard and how difficult is it to find the right flooring system? Steven Argent, Construction Director at fit-out specialists QOB Interiors, looks at the WELL Standard and taking a healthy view in the specification of a flooring system.
When you consider the average person spends well over 90% of their life in and around buildings, the creation of a healthy environment will have a direct impact on their wellbeing. Illness costs UK businesses on average £550 per employee per year, amounting to a staggering £30 billion annually, according to the Chartered Institute of Professional Development, so incorporating wellbeing into our buildings has never been more important.
Putting the emphasis on the human element, WELL is a performance-based system for measuring, certifying, and monitoring features of the built environment that impact human health and wellbeing through air, water, nourishment, light, fitness, comfort and mind.
While the building industry is used to dealing with and incorporating well factors such as light and air quality, other features that impact mobility, access, nutrition, access to water, to name but a few - are new territory for many designers and fit-out specialists. This innovative approach to building design and operation is set to change the way we create building interiors.
A well-made floor
Whether it's contributing to air quality and sound reduction, adding to atmosphere or helping to create a hygienic environment, floors play a significant and increasingly important role in a healthy and productive environment. A well-chosen floor can add texture and comfort, whilst having the capability to reflect light and delineate spaces as well. To meet the WELL standard, it's important to choose flooring manufacturers offering products that contribute to the health and wellbeing of building occupants. A flooring manufacturer which offers low VOC, phthalate-free products and solutions which are sound-reducing and allergy approved will make a significant contribution towards creating a healthier workplace and meeting WELL certification.
One Carter Lane
The first project in Europe to achieve the standard is One Carter Lane, the London office of multi-disciplinary engineer Cundall. As the first building in Europe to be delivered under WELL, there was careful attention to the specification of every single material and product used to ensure it met the criteria of WELL.
This included research, testing materials as well as checking credentials and conformity. It is surprising when you start to scrutinise products how difficult it can be to find materials that are natural and don't contain any toxins. It's vital specifiers think carefully about what is used and the long term effects this has on building occupiers.
From a design by architects Studio Ben Allen, the challenging 15,400 sq ft Cat B commercial office fit-out was carried out to stringent tolerances with a focus on the most sustainable and environmentally-friendly materials. Every aspect of the ground floor fit-out by QOB – from materials used, to lighting, heating and open space – had to be thoroughly considered as to the impact on post-occupancy use before the design was finalised.
The specification of materials under WELL meant only those that had a very low concentration of formaldehydes and volatile organic compounds (VOC) could be used. The VOC rating of all materials had to be between negligible and zero, ensuring that office fixtures, fittings and fabric did not expel harmful chemical or organic emissions. Medical research has shown that indoor air quality has a major influence on the health, wellbeing and productivity of building occupants.
A floor like no other
At the Cundall offices, all furnishings, insulation, interior paint, adhesives, oils, waxes, varnishes and finishes were specified for low or zero VOC, formaldehyde and toxic content. A recycled, woven nylon floor tile from a Swedish manufacturer was specified for the flooring in main office area and fitted to the raised access floor system with an ultra-low VOC adhesive.
The flooring material used in the main office area is from Bolon's Botanic selection and is a natural Bolon tile. This particular product aids the reduction of VOC absorption which makes it the perfect fit for this environmentally aware fit out.
The solvent-free adhesive used for bonding the floor tiles has an extremely low emission level of VOCs which makes it harmless for those who apply the product and for the people work in the environment in which it is applied. In addition, a WELL approved anti-slip, noise-absorbent and easy to maintain satin rubber floor was used for the tea point area. This was also applied used the ultra-low VOC adhesive.
As a preventative measure, during construction, the specialist contractor ensured that all the carpet tiles were kept protected in the secure site office, to further reduce the chance of VOC's absorption.
Managing the fit-out meant ensuring there was an understanding of product selection on the site so that operatives couldn't defer away from using the approved materials. This was achieved through specific site inductions, informing the installation teams of the environmental standards to be achieved and their contribution to achieving them.
Furthermore it was vital that the selected environmentally accredited materials performed to ‘industry standards' so as to dispel the common myth that there would be a noticeable loss of performance. This was achieved through the ridged review of manufacturer's material data sheets and ‘benchmarking' the install to observe quality of workmanship and the acceptable performance of the installation prior to continuing with the whole install.
With the constant monitoring and testing of indoor air quality under WELL so critical throughout the fit-out, it was vital there were precautions in place to isolate work areas to ensure any dust was contained, preventing contamination entering into other areas of the site. In addition, dust covers were used on light fittings and airtight plastic covers on all grills, filters, ducts and fan coil units.
The WELL Building Standard is uncharted territory for many across the industry, but at One Carter Lane, Cundall has an office environment that sets a high benchmark for the workplace, putting people's health and wellbeing at the very heart of the building.
Visit: http://qobinteriors.com/
Additional Blogs
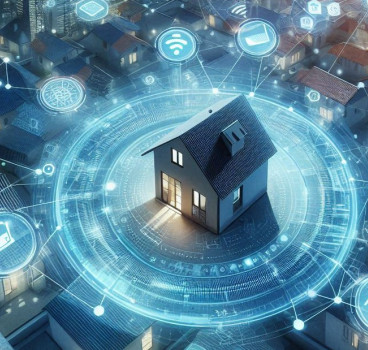
BEMS - the perfect fit for the UK’s retrofitting programme
While the Future Homes Standard (FHS) is exacerbating the need for property developers and house builders to incorporate energy efficient and sustainable technologies and materials into new build...
Read moreHow Sustainable Drainage Systems (SuDS) are changing UK construction standards
For decades, drainage in UK construction has largely relied on traditional pipe systems designed to move rainwater quickly away from homes and roads into sewers. But with climate change bringing...
Read more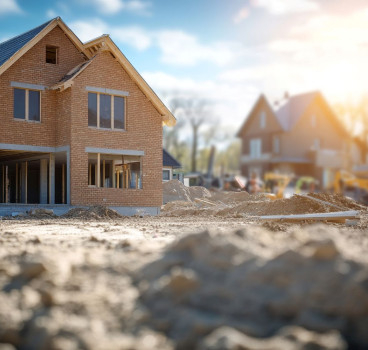
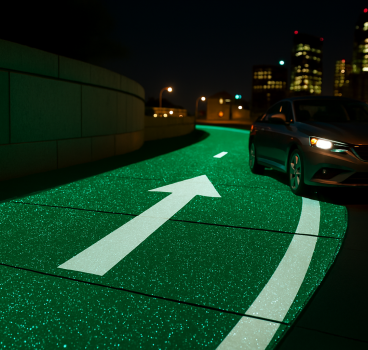
Why glow-in-the-dark concrete is a material for the future
Concrete is the backbone of modern civilisation and is one of the most widely used man-made materials on Earth, but for all its strength and versatility, concrete has never been thought of as...
Read more