Dry fixing means quick clean roof installation
The move towards mortar-free, dry fix roof and drainage solutions has made it quicker, easier and safer to install throughout the build process. Offering a wealth of benefits to the installer and homeowner, Hayley Lowry, Marketing Manager of Ariel Plastics outlines the dry-fix options for new-build projects and how these systems are the simple, cost-effective, low maintenance route to a weathertight roof, whatever the elements have in store.
Dry fix roofing is the term used to describe the mechanical fixing of roofing materials. Traditional mortar bedding is still the most widely-used fixing method in England and Wales, in contrast to Scotland, where 80% of roofing is already mechanically-fixed. However, the increased incidence of storms during recent years has clearly highlighted the unreliability of mortar. The switch to dry fix roofing in Britain and Ireland is well established but looks set to gather even greater momentum. Considering all the advantages, it is not difficult to see why.
The roof is the most exposed part of any building. Using mortar to secure vulnerable areas of the roof, such as the verge, will inevitably lead to future maintenance. Differential movement causes mortar to crack and no reliance should be placed on its tensile or shear strength. The action of frost and rain will exploit the development of hairline cracks.
In contrast, because dry fix roofing is mechanically-fixed it offers improved safety, security and increased resistance to wind uplift and water penetration. Dry fixing is a year-round solution; it can be carried out in damp and freezing conditions. A fast and simple process, it's a method that eliminates the need for mix-and-apply mortar and its incurring mess. Special skills and tools are not required to dry fix, making it highly cost-effective. It also complies with BS 5534, a new code of practice that details design standards, performance and installation of pitched roofs and vertical cladding using slates, tiles and wooden shingles.
Regulation change
BS 5534 came into force in February 2015 and outlined a number of changes including the use of mortar, which can no longer be used in isolation to fix ridges and hips. These should now also be mechanically-fixed. Fixing requirements for roof tiles have been increased in the latest code of practice which also requires all single-lapped tiles on a roof to be mechanically-fixed. It also states perimeter tiles should now have a minimum of two fixings. In addition, testing bodies now have to assess the measurement of the wind uplift resistance of underlays.
The Construction (Design and Management) Regulations place a duty of care on designers to select building components that minimise health and safety risks, not only during construction, but during future maintenance. The use of dry fix roofing eliminates the need to repair failed mortar bedding, therefore avoiding future maintenance work and improving safety on site. In terms of dry fix options, mortar-freeproducts which provide a unique jointing system and can be used with half-round and angled ridges are ideal for this practice. This is not only the quickest method of installing ridge tiles to a roof; it produces a neat ridge line of traditional appearance whilst also providing high-level ventilation.
Product options
For dry verge, the ideal products are ones which enable verge tile fixing without the need for mortar whilst protecting verge tiles from wind uplift, pest infestation and weather degradation. Most systems are universal and come in a range of colours to blend with most tiles, slates and bargeboards. With the UK experiencing more frequent extreme weather conditions, greater responsibility has been placed on the roofing underlay to cope with increasing wind forces. The potential effect of an underlay subjected to excessive wind loading is for it to balloon upwards potentially causing the tiles or slates to dislodge. This issue has been addressed in the latest revision to BS5534: 2014 Code of Practice for Slating and Tiling. Effective from March 2015, the guidance outlines the minimum requirements for taping the side laps of roofing underlays dependent on the exposure of the roof to wind uplift, batten gauge and the underlay selected. In addition to the prevention of wind uplift, the taping of side laps of roofing underlays helps improve the thermal performance of a building by reducing air filtration and convective heat loss.
Dry fix valleys are another product option. Fully-weatherproof options manufactured from GRP are now available offering a cost-effective alternative to lead. Dry fixing of valley troughs is quicker, less dependent on site skills and guarantees a neater finish than mortar bedding. Slate, tile and ridge vents are available to install mechanically on the roof without the need for mortar. Similarly, a wide range of eaves ventilation products are available to mechanically fix: eaves vent kits, rafter and fascia trays, over fascia vents and soffit vents.
With availability of so many proven products, it's no wonder the construction industry is rapidly turning to dry fix products as the quick, easy-to-apply, cost-effective solution for weathertight roofing.
Additional Blogs
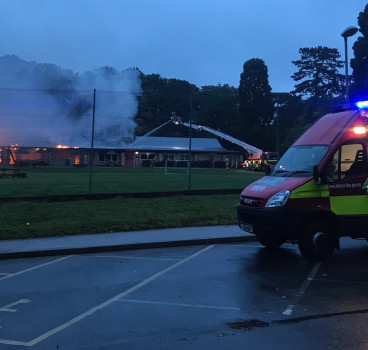
Back to school and the same old story on fire safety
We are about to start another school year and once again, we find ourselves having the same discussion about fire safety guidance for schools. The last attempt to revise Building Bulletin 100 (BB100)...
Read moreBEMS - the perfect fit for the UK’s retrofitting programme
While the Future Homes Standard (FHS) is exacerbating the need for property developers and house builders to incorporate energy efficient and sustainable technologies and materials into new build...
Read more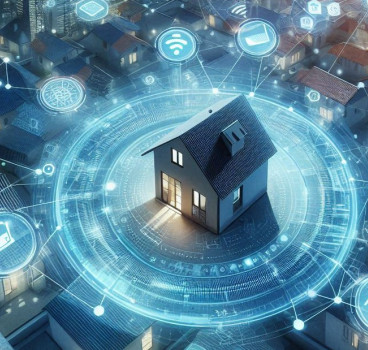
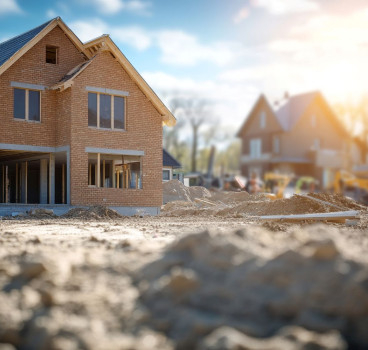
How Sustainable Drainage Systems (SuDS) are changing UK construction standards
For decades, drainage in UK construction has largely relied on traditional pipe systems designed to move rainwater quickly away from homes and roads into sewers. But with climate change bringing...
Read more