Dry construction and a future with no concrete, no plaster and no mortar
For decades, the construction industry has relied on water-intensive processes to build the homes, schools, hospitals and infrastructure that shape our lives. Wet concrete, plaster, mortar and other traditional materials are the backbone of the built environment, but with climate change, urbanisation and sustainability - driving a new wave of innovation – there is now a real alternative and it’s called dry construction, writes John Ridgeway.
Dry construction refers to a set of building techniques that eliminate the need for water-based materials and lengthy curing times. Instead, these systems rely on prefabricated components, mechanical fastenings and modular solutions. The result? Faster build times, cleaner sites, reduced environmental impact and greater adaptability for modern needs. It’s already happening around the globe and if current trends continue, the "no-wet" construction approach could soon become the norm.
One of dry construction's most obvious benefits is its speed. With no waiting time for concrete to cure or plaster to dry, dry methods allow for much faster project turnaround. Structural framing, walls, ceilings and floors can be assembled in days instead of weeks, especially when prefabricated off-site.
This is especially valuable in disaster relief housing, where time is critical, commercial developments with tight completion schedules and urban infill sites with limited access or time restrictions. By reducing dependency on weather conditions, especially rain and cold, dry construction minimises site delays to keep projects on track.
The added bonus is that dry construction aligns with a broader push toward sustainability and net-zero carbon goals. Water scarcity is a growing concern in many parts of the world. Dry systems obviously eliminate the need for water-intensive mixes and curing, helping conserve this vital resource.
Furthermore, materials such as cross-laminated timber (CLT), steel framing and structural insulated panels (SIPs) have lower embodied carbon footprints compared to traditional concrete. With less dust, debris and runoff, dry construction also leads to cleaner, safer worksites and less waste sent to landfills. In addition, dry components are typically modular and mechanically fastened and can often be disassembled and reused at the end of a building's life.
Dry construction around the world
Dry construction is not a theoretical concept - it's already being implemented in a wide number of innovative ways across different regions. Germany and Austria have been early adopters of timber construction, particularly CLT. High-performance wood buildings are being used for schools, residential buildings, and commercial offices. Following earthquakes, Japan has adopted lightweight, modular dry construction systems to rapidly house displaced populations. The focus is on seismic safety and speed.
Facing enormous demand for affordable housing, India is trialling precast panels, GFRG (Glass Fibre Reinforced Gypsum) walls and other dry technologies to accelerate mass housing projects. Countries like Norway and Sweden are leaders in dry construction, particularly timber, mainly due to regulations and other incentives, which promote low-carbon building practices and prefabrication. The U.S. is also seeing increased interest in modular hotel construction, container homes and off-site fabricated units, especially in cities with housing shortages like New York and San Francisco.
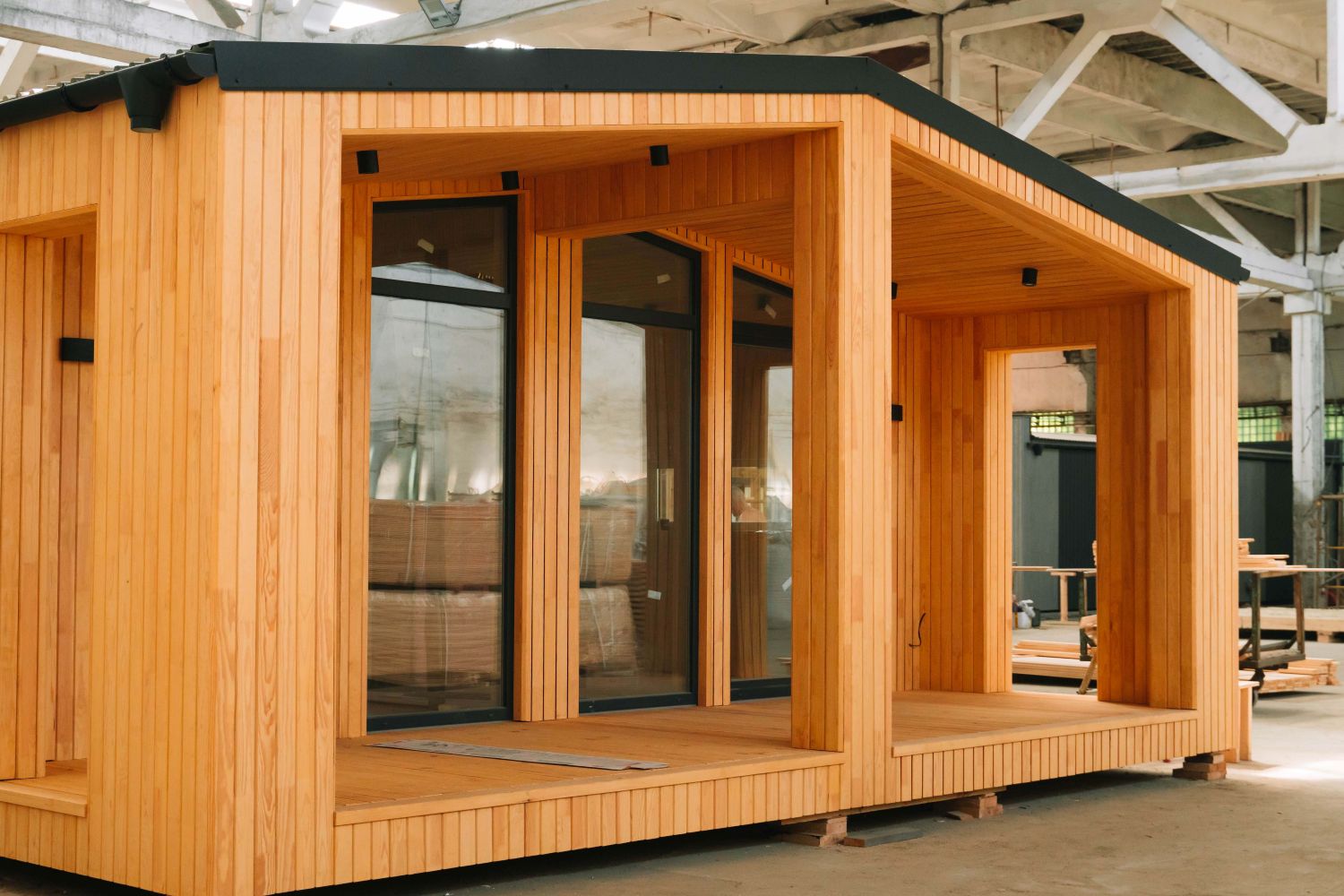
But what makes dry construction work? Steel and timber framing are setting the pace. Lightweight yet strong, these framing systems can be quickly assembled on-site and customised to meet seismic or wind resistance needs. Ready-to-install gypsum boards and wall systems are eliminating the need for wet plaster, enabling faster room partitioning. Entire rooms or building sections are being manufactured off-site, delivered to where they are needed and installed like Lego blocks.
Dry screeds and structural insulated panels (SIPs) offer thermal efficiency with easy installation, making them ideal for energy-conscious buildings. Instead of adhesives and mortars, mechanical clips, screws and brackets are now being increasingly used to hold everything in place, allowing for easy adjustments and disassembly.
Obstacles and limitations
Despite its benefits, dry construction is not without its challenges. Initial material costs can be higher, especially for high-performance panels or custom prefab modules. However, life-cycle savings often outweigh upfront investment. In many regions, the labour force is still trained in traditional wet methods, so shifting to dry construction requires retraining and new certifications.
In addition, building codes in some areas have not yet adapted to dry systems. Approvals and inspections can be slower due to unfamiliarity with these techniques. Some developers also view dry construction as “experimental” or less robust, especially in markets where concrete is seen as the gold standard.
In spite of these challenges, dry construction continues to evolve, with several emerging trends. AI and parametric design tools can now generate optimal building layouts tailored for prefabricated and modular systems, reducing waste and increasing efficiency. On-site robots and automated machinery are also beginning to handle dry component placement, from steel framing to panel installation, improving precision and safety.
In addition, researchers are developing materials that change shape, conduct air, or self-heal, all potentially applicable to dry assembly systems. Some developers are also experimenting by combining dry methods with new low-carbon concretes and bio-based binders to create hybrid systems that balance flexibility and strength.
Who stands to benefit most?
Fast-track builds and reduced site disruption make dry construction particularly ideal for suburban and urban housing developments. Minimising site noise, dust and disruption is crucial for schools and hospitals, so dry methods are perfect here. Quick deployment of safe, energy-efficient structures is also invaluable during humanitarian crises and post-disaster recovery. Furthermore, those committed to sustainability can use dry techniques to reduce carbon footprints, incorporate circular economy principles and pursue high green building ratings.
In an industry often slow to change, dry construction offers a bold reimagining of how we build. It's faster, cleaner and more aligned with the environmental and social demands of the 21st century. While challenges remain, the benefits are clear - less water, lower emissions and structures that go up in days, not months.
As materials, policy, and public awareness evolve, dry construction is poised not just to complement traditional methods, but to replace them altogether in many contexts. For architects, engineers and builders, the message is simple - the future is dry - and it's already here.
Additional Blogs
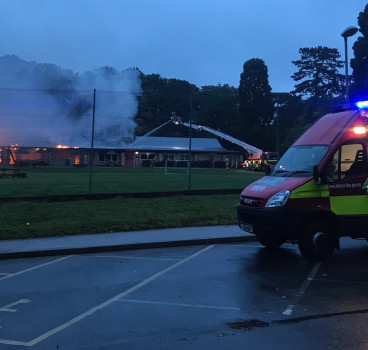
Back to school and the same old story on fire safety
We are about to start another school year and once again, we find ourselves having the same discussion about fire safety guidance for schools. The last attempt to revise Building Bulletin 100 (BB100)...
Read moreBEMS - the perfect fit for the UK’s retrofitting programme
While the Future Homes Standard (FHS) is exacerbating the need for property developers and house builders to incorporate energy efficient and sustainable technologies and materials into new build...
Read more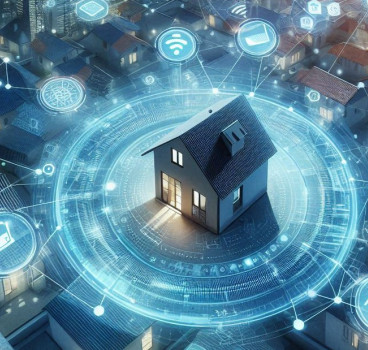
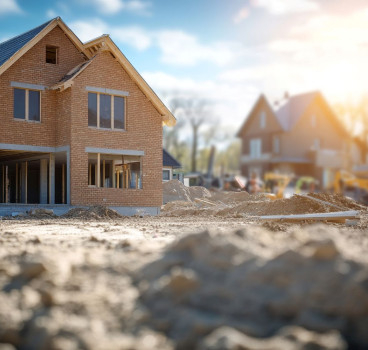
How Sustainable Drainage Systems (SuDS) are changing UK construction standards
For decades, drainage in UK construction has largely relied on traditional pipe systems designed to move rainwater quickly away from homes and roads into sewers. But with climate change bringing...
Read more