Does green steel represent a sustainable future for construction?
Steel and its strength, durability and versatility has made it an indispensable material for centuries, yet, it comes at a significant environmental cost. Traditional steel production is a major emitter of carbon dioxide, contributing a substantial percentage of global greenhouse gas emissions. But as the world grapples with the urgent need for decarbonisation, the spotlight is increasingly turning towards a revolutionary concept - green steel, writes John Ridgeway.
Green steel represents a fundamental shift in how steel is made, aiming to drastically reduce or even eliminate the carbon footprint associated with its production and revolves around significantly lowering or eliminating carbon dioxide (CO2) emissions during the manufacturing process. This goes beyond simply recycling scrap metal, although that is an important aspect of a circular economy for steel. True green steel production more often involves a combination of innovative technologies and a commitment to sustainable practices throughout the entire value chain.
Key approaches to producing green steel include the use of hydrogen-based direct reduced iron (DRI), a method which replaces carbon-intensive coking coal, traditionally used to remove oxygen from iron ore in blast furnaces. When hydrogen reacts with iron ore, the byproduct is water (H2O) instead of CO2, drastically reducing emissions. This is considered by many to be the most promising pathway to near-zero emission primary steel production.
Electric arc furnaces (EAFs) powered by renewable energy are another method. EAFs primarily melt down scrap steel to produce new steel. When these furnaces are powered by 100% renewable energy sources like solar, wind, or hydropower, the associated emissions are significantly reduced compared to traditional blast furnace methods that rely on fossil fuels.
While not eliminating emissions at the source, CCUS technologies capture the CO2 produced during conventional steelmaking and either store it underground or utilise it in other industrial processes. This can be a transitional technology to reduce the immediate impact of existing infrastructure. Replacing fossil fuels with sustainably sourced biomass or other low-carbon fuels in various stages of the steelmaking process can also contribute to emissions reduction.
It's important to note that the "greenness" of steel can be measured in various ways, including the total product carbon footprint (PCF), which accounts for emissions throughout the entire lifecycle, including raw material extraction and transportation. Certifications and transparent reporting are crucial for differentiating truly green steel from products with marginal improvements.
The pioneers of green steel
Several companies around the world are already at the forefront of developing and commercialising green steel technologies. These pioneers are investing heavily in research, development and pilot projects to bring low-carbon steel to the market:
- SSAB (Sweden): Through their HYBRIT (Hydrogen Breakthrough Ironmaking Technology) project, in collaboration with LKAB and Vattenfall, SSAB aims to produce fossil-free steel using 100% hydrogen-based DRI. They have already produced the world's first fossil-free steel and are working towards industrial-scale production.
- H2 Green Steel (Sweden): This ambitious newcomer is building a fully integrated, digitalised, and circular steel plant in Northern Sweden, powered by green hydrogen. Their goal is to produce near-zero emission steel at scale, targeting the automotive and construction industries.
- Boston Metal (USA): This company is developing a Molten Oxide Electrolysis (MOE) technology that uses electricity to directly reduce iron ore, eliminating the need for coal and producing only oxygen as a byproduct.
- ArcelorMittal (Global): As one of the world's largest steel producers, ArcelorMittal has launched its XCarb™ initiative, which encompasses various low-carbon steelmaking routes, including hydrogen DRI and carbon capture technologies, with a goal of achieving carbon neutrality by 2050.
- Voestalpine (Austria): This steelmaker is actively researching and developing various green steel technologies, including hydrogen-based methods and the use of electric arc furnaces with renewable energy.
- JSW Steel (India): JSW Steel is exploring various pathways to reduce its carbon footprint, including increasing the use of renewable energy and investing in research into hydrogen-based steelmaking.
- Nippon Steel Corporation (Japan): This major steel producer is also committed to carbon neutrality by 2050, focusing on hydrogen-based steelmaking and carbon capture technologies.
- Blastr Green Steel (Norway/Finland): Blastr is building an integrated value chain to produce ultra-low CO2 steel using hydrogen-based DRI, targeting the European automotive and construction markets.
- Stegra (formerly H2 Green Steel): Focused on large-scale green hydrogen production to fuel their near-zero emission steel plant in Sweden.
These are just some of the key players and the landscape is rapidly evolving with new initiatives and collaborations emerging globally. The competition and innovation in this space are crucial for driving down the cost and scaling up the production of green steel.
Green steel and the construction industry
The construction industry is a significant consumer of steel, accounting for a substantial portion of its global demand. It is also under increasing pressure to reduce its environmental impact, with embodied carbon in materials becoming a key focus. Green steel offers a powerful solution to decarbonise this vital sector.
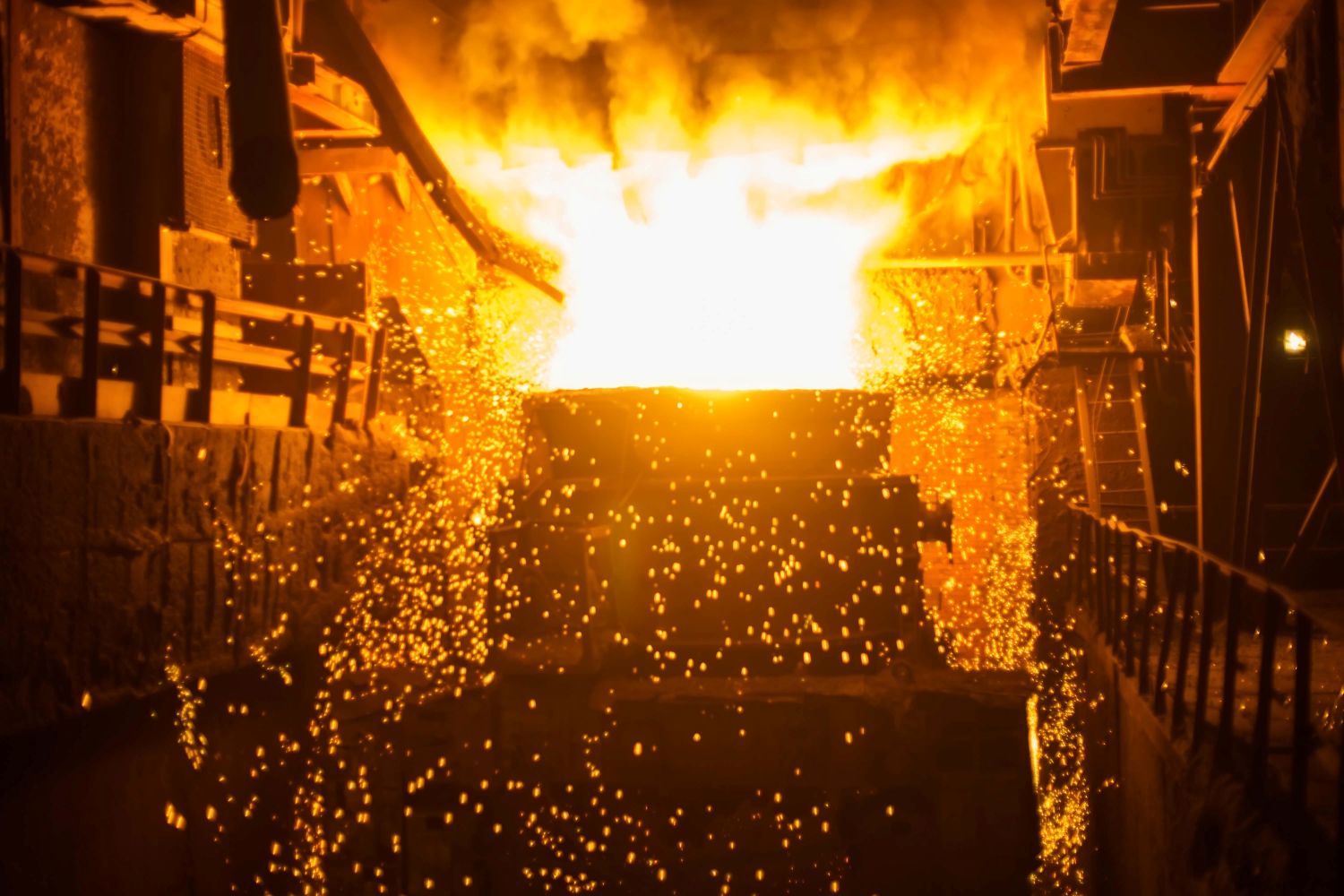
By using green steel in construction projects, the embodied carbon - the greenhouse gas emissions associated with the extraction, manufacturing, transportation, and end-of-life stages of building materials - can be drastically reduced. This is crucial for achieving net-zero carbon buildings and infrastructure.
Furthermore, as regulations and green building certifications (like LEED and BREEAM) increasingly emphasise embodied carbon, green steel will become essential for projects aiming for high sustainability ratings. Investors are also increasingly prioritising projects with strong environmental credentials. The use of green steel can make construction projects more attractive to green financing and impact investment.
There is no doubt that companies in the construction sector are facing growing pressure from stakeholders to demonstrate their commitment to sustainability. Using green steel aligns with these CSR goals and enhances brand reputation. The potential for lower-carbon structural elements could also inspire innovative building designs and construction techniques.
Green steel production often emphasises the use of recycled scrap, contributing to a more circular economy for steel and reducing the reliance on virgin resources. However, green steel may come with a price premium due to the costs associated with new technologies and production processes, but as production scales up and demand increases, these premiums are expected to decrease. Some clients may also be willing to pay a premium for truly green materials to meet their sustainability goals.
Types of green steel products for construction:
One of the reasons is because the versatility of steel means that green steel can be used in a wide range of construction products, essentially mirroring the applications of conventional steel such as beams, columns and other load-bearing elements for buildings, bridges and infrastructure. This is a major area where the impact of green steel can be significant in reducing embodied carbon.
Reinforcing steel (Rebar), used to strengthen concrete structures, produced with lower emissions will also be crucial for decarbonising concrete construction. Furthermore, steel frames and cladding for industrial buildings, warehouses and even residential structures, can significantly lower the carbon footprint. Add on steel decking, pipes and tubes, façades, modular construction components and everything else from bridge supports to railway tracks and energy infrastructure, then green steel has a vital role to play.
Despite the immense potential, the widespread adoption of green steel in the construction industry still faces challenges. Current green steel production capacity is still relatively small compared to traditional methods. Scaling up production to meet the demands of the construction sector will require significant investment and technological advancements.
Green steel production, especially through hydrogen-based DRI, can also be more expensive in the initial stages. Achieving cost parity with conventional steel will be crucial for widespread adoption. Furthermore, establishing reliable and efficient supply chains for green steel products will be essential for the construction industry to readily access these materials.
However, the momentum behind green steel is undeniable. Growing environmental awareness, stricter regulations, increasing demand from end-users and the commitment of pioneering steelmakers are driving progress. Collaboration across the entire value chain, from steel producers to architects, engineers, contractors and policymakers, will also be crucial to overcome the challenges and unlock the transformative potential of green steel for a more sustainable construction industry and a greener future for all.
Additional Blogs
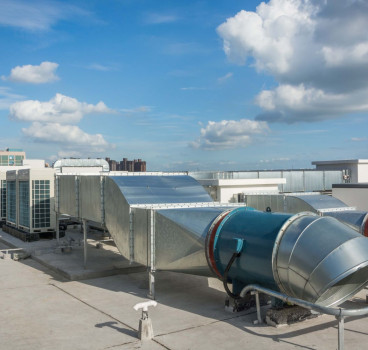
The fight for facades or why M&E must shape early design decisions
With sustainability and energy efficiency, not to mention decarbonisation, increasingly taking priority during building design, MEP engineers and architects are coming into conflict as part of an...
Read moreBack to school and the same old story on fire safety
We are about to start another school year and once again, we find ourselves having the same discussion about fire safety guidance for schools. The last attempt to revise Building Bulletin 100 (BB100)...
Read more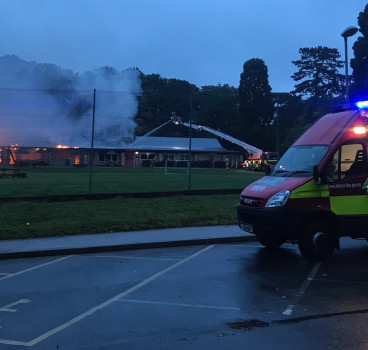
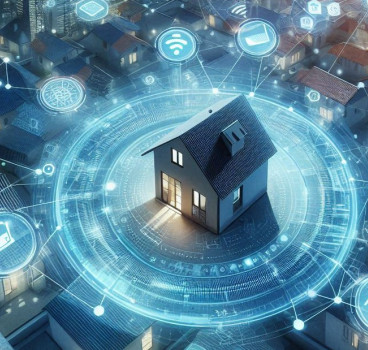
BEMS - the perfect fit for the UK’s retrofitting programme
While the Future Homes Standard (FHS) is exacerbating the need for property developers and house builders to incorporate energy efficient and sustainable technologies and materials into new build...
Read more