Building boom or carbon doom? The debate continues
The construction industry is booming. Cities are expanding, infrastructure needs are growing and the demand for new, energy-efficient buildings is at an all-time high. However, this progress comes at a hidden cost – a massive carbon footprint. While energy-efficient buildings are crucial for tackling climate change, a new challenge is emerging - embodied carbon. This refers to the greenhouse gas emissions associated with the entire lifecycle of a building, from material extraction and construction to eventual demolition – and it is creating a major debate, writes John Ridgeway.
The dilemma lies in prioritising which carbon footprint to tackle first. Should the focus be on minimising the embodied carbon associated with materials and construction methods, or on reducing the operational carbon generated by building energy use? Each approach has its merits and drawbacks, creating a complex equation for architects, engineers and policymakers grappling with building a sustainable future.
Advocates for prioritising embodied carbon argue that these emissions are "locked in" from the outset. Choosing low-carbon materials like recycled steel or sustainably harvested wood has a lasting positive impact. Additionally, with rapid technological advancements, improving building energy efficiency in the future becomes a possibility.
Focusing on operational carbon first, offers the potential for quicker results, however, longer term, investing in energy-efficient technologies and renewable energy sources can yield significant reductions in a building's carbon footprint throughout its operational lifespan.
So, we can see that the embodied vs. operational carbon debate is far from a binary choice. Finding the optimal solution lies in a lifecycle approach that considers both aspects and needs a holistic strategy that requires innovative thinking and collaboration across the entire construction supply chain.
Quantifying the carbon footprint
The logical first step towards achieving a balance involves Life Cycle Assessment (LCA). This methodology allows architects and engineers to quantify the embodied and operational carbon footprint of different design options, taking into account factors such as material extraction and processing. The energy consumption and emissions associated with on-site activities like welding, cutting and using heavy machinery also have to be factored in.
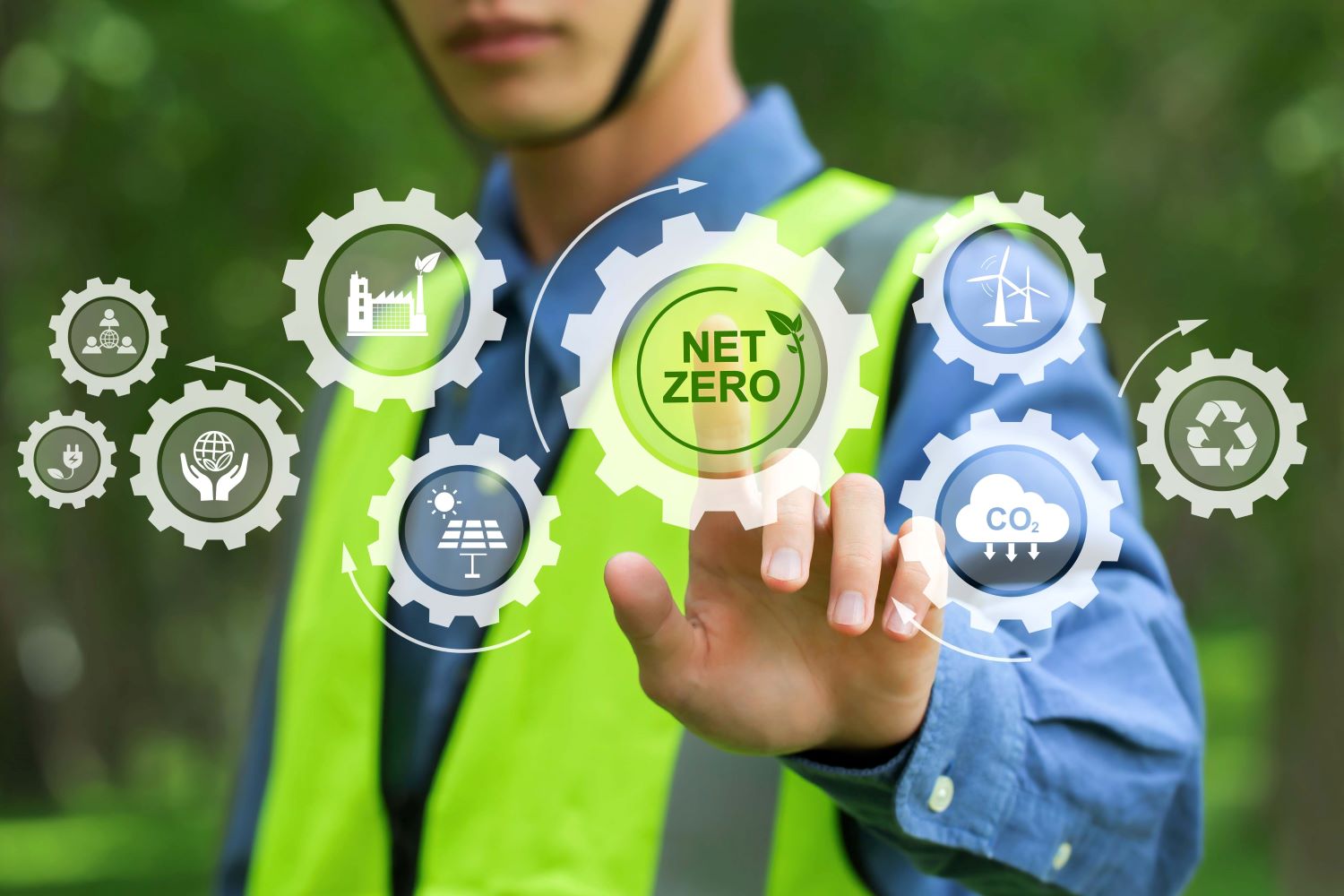
The energy efficiency of the building envelope (walls, roof, windows) and the use of passive heating and cooling strategies have to be evaluated together with the efficiency of heating, ventilation and air conditioning systems, which have to be considered, along with the potential for integrating renewable energy sources such as solar panels.
Other factors include the projected energy consumption for heating, cooling, lighting, and end-of-life deconstruction and disposal, factoring in the environmental impact of demolition and waste management.
By conducting a comprehensive LCA assessment, stakeholders can compare different design options and construction methods, prioritising those with the lowest overall carbon footprint throughout the building's lifecycle.
Innovation for a sustainable future
The good news is that the construction industry is not without solutions. A growing market of low-carbon building materials offers alternatives with a significantly smaller environmental footprint. Examples include recycled steel, sustainably harvested wood and bio-based materials like bamboo are gaining traction.
Prefabricated construction methods involving assembling building components off-site in a controlled environment, are also helping to reduce waste, improve material efficiency and potentially lower embodied carbon compared to traditional on-site construction.
Implementing circular economy principles in construction also promotes the reuse and repurposing of building materials. This can involve deconstructing existing structures and salvaging materials for use in new buildings, minimising the need for virgin materials and their associated embodied carbon.
Building automation systems, smart sensors, and Internet of Things (IoT) applications can optimise building energy use and improve operational efficiency and when combined with renewable energy sources like solar panels, wind turbines, or geothermal systems we can drastically reduce reliance on fossil fuels.
Collaboration is key
Achieving a sustainable future for construction requires a collaborative effort from all stakeholders. Design professionals in particular, need to integrate LCA principles into the design process, prioritising low-carbon materials and energy-efficient building systems.
Manufacturers also have a crucial role to play in developing and promoting sustainable building materials with a lower embodied carbon footprint. Construction companies need to adopt best practices to minimise waste and optimise on-site resource utilisation during the construction phase – and most important of all – we need more Government policies that incentivise low-carbon building practices.
Challenges and opportunities
Despite the encouraging advancements, challenges remain on the path towards sustainable construction. Comprehensive data on the embodied carbon footprint of various materials and construction methods is still evolving. This mean that we need increased transparency and standardisation to facilitate informed decision-making.
While low-carbon solutions are rapidly evolving, the upfront cost of sustainable materials and technologies can be higher than conventional methods and this means that construction professionals continue to opt for cheaper alternatives. Incentives, tax breaks and financing mechanisms need to be introduced to help bridge the cost gap and encourage wider adoption.
Because traditional procurement practices often prioritise the lowest initial cost, we need a fundamental shift towards a lifecycle cost perspective that considers both embodied and operational carbon over the entire building lifespan.
The construction industry has a significant opportunity to be a leader in environmental stewardship. By addressing both embodied and operational carbon, the industry can create buildings that are not only energy-efficient but also minimise their environmental impact for generations to come.
This requires a holistic approach, continuous innovation, and collaboration across the supply chain. As the industry embraces sustainable practices, the future of construction can be one where buildings are not just symbols of progress, but also beacons of environmental excellence.
Further reading
We would recommend further reading based on the Dutch Approach: The Netherlands has implemented ambitious embodied carbon reduction policies in the construction sector. Regulations aim to reduce embodied carbon in new buildings by 80% by 2030 compared to 2013 levels. You can down load the PDF by clicking the link: (https://www.dgbc.nl/upload/files/Circulariteit/BuildingLife/Position%20Paper%20Whole%20Life%20Carbon_EN.pdf)
Additional Blogs
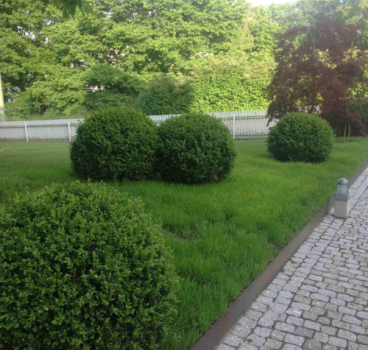
Why healthy soil is the hidden key to quality homes
Across countless new housing developments, a hidden problem is undermining quality and driving up customer complaints - and most housebuilders will never see it coming. The issue is not the homes...
Read moreThe fight for facades or why M&E must shape early design decisions
With sustainability and energy efficiency, not to mention decarbonisation, increasingly taking priority during building design, MEP engineers and architects are coming into conflict as part of an...
Read more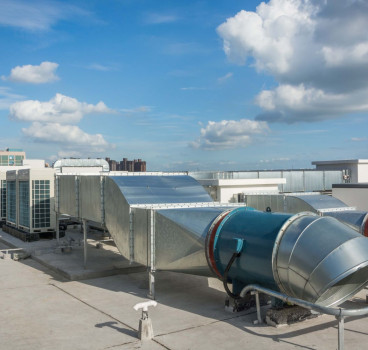
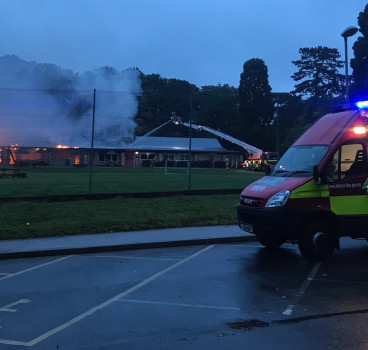
Back to school and the same old story on fire safety
We are about to start another school year and once again, we find ourselves having the same discussion about fire safety guidance for schools. The last attempt to revise Building Bulletin 100 (BB100)...
Read more