Talk.Build - for the best Commercial Construction Blogs
Looking for the best construction blogs to stay ahead of the curve in the ever-evolving built environment? Talk.Build is your ultimate destination with thousands of different commercial construction blogs to choose from, with more added nearly every day. We serve as a vibrant online forum, to help foster knowledge and exchange views between seasoned industry veterans, emerging talents, and passionate construction enthusiasts.
Check out our extensive Commercial Blog Library: Dive into our expansive library featuring thousands of commercial construction blogs, meticulously categorized and continually updated with fresh content. Diverse Subject Matter: Explore a comprehensive range of topics spanning project management, safety regulations, sustainable construction practices, and cutting-edge building technologies. Expert-Driven Insights: Gain invaluable knowledge from industry leaders who share their practical experience with materials, tools, construction techniques, current design trends, and successful business strategies.
Check out The Feed for construction news in real time.
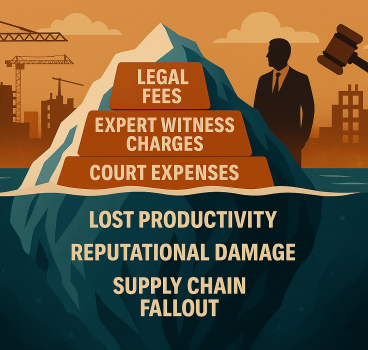
The true economic cost of construction disputes
Disputes are an almost inevitable, albeit undesirable, feature of modern construction. When such disagreements escalate to formal dispute resolution mechanisms, particularly litigation, the immediate...
Read moreThe time to ensure a brighter and greener future is now
With the UK seeing a surge in business owners prioritising sustainability and adopting new technologies, the building energy management systems (BEMS) sector is ideally positioned to take advantage....
Read more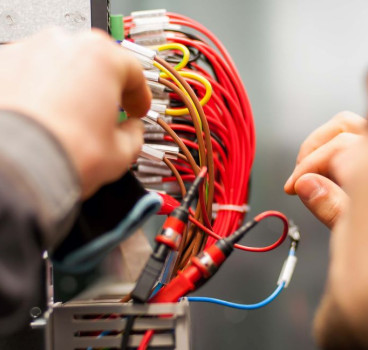
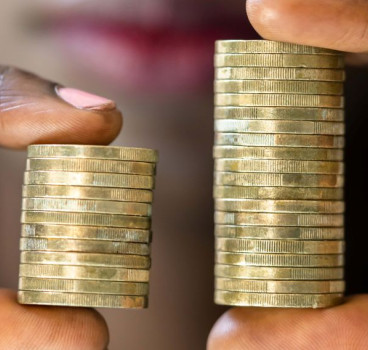
Addressing gender pay disparity in the construction industry
The construction sector globally faces a persistent challenge in achieving equitable pay for its female workforce. Despite increasing recognition of the value of diversity, women in construction...
Read moreWhy Europe is falling behind in the race to build data centres
Data centre infrastructure is proceeding at an unprecedented rate, driven by the exponential growth in data generation. Countries and regions worldwide are actively competing to host the next...
Read more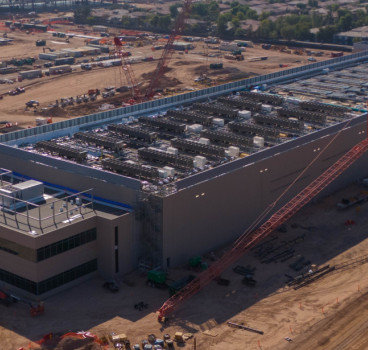

Why civil engineering is the foundation for smart cities
Rapid urbanisation and technological advancement are transforming cities into "smart cities." These environments use interconnected technology and data to optimise resource management, enhance public...
Read moreWhy you need an old-fashioned surveyor to question digital accuracy
The contemporary construction and engineering landscape is increasingly defined by technology. Drones map vast terrains in minutes - LiDAR scanners capture intricate geometries with unprecedented...
Read more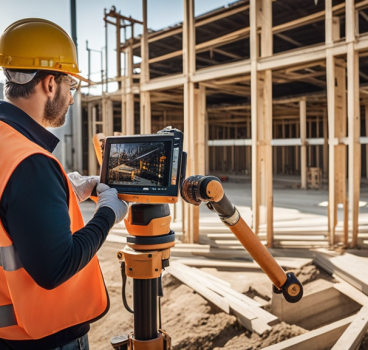
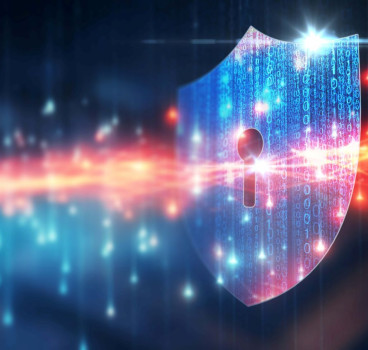
What will be the ethics of AI in construction?
The integration of Artificial Intelligence (AI) into the construction industry promises much. From AI-driven scheduling and predictive analytics for material procurement to automated quality control...
Read moreThe unseen construction principles behind data centres
In an increasingly digitised global economy, data centres represent the physical bedrock upon which all modern connectivity, commerce and communication rest. While their services - cloud computing,...
Read more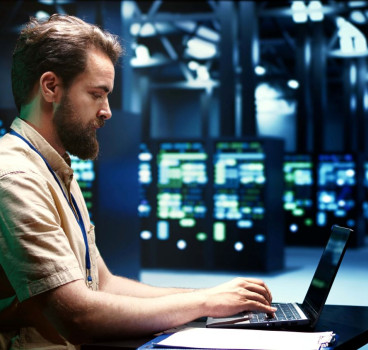
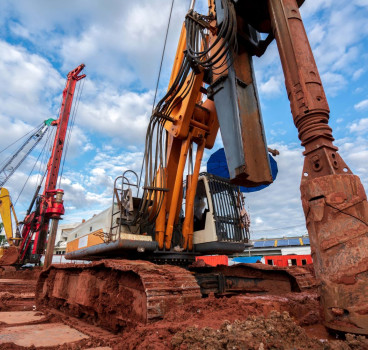
Why Near-Miss Reporting is Valuable for Proactive Safety Measures
Construction is one of the most hazardous sectors globally, consistently ranking high for workplace injuries and fatalities. However, many serious incidents are preceded by close encounters with...
Read more