Talk.Build: Your One-Stop Shop for the best Construction Blogs
Looking for the best construction blogs to stay ahead of the curve in the ever-evolving built environment? Talk.Build is your ultimate destination with thousands of different construction blogs to choose from, with more added nearly every day. We serve as a vibrant online forum, to help foster knowledge and exchange views between seasoned industry veterans, emerging talents, and passionate construction enthusiasts.
Unparalleled Depth and Breadth of Construction Content:
Extensive Commercial Blog Library: Dive into our expansive library featuring thousands of construction blogs, meticulously categorized and continually updated with fresh content. Diverse Subject Matter: Explore a comprehensive range of topics spanning project management, safety regulations, sustainable construction practices, and cutting-edge building technologies. Expert-Driven Insights: Gain invaluable knowledge from industry leaders who share their practical experience with materials, tools, construction techniques, current design trends, and successful business strategies.
Stay Informed: We choose the best construction blogs to keep you abreast of the latest industry news, emerging trends, and groundbreaking innovations shaping the future of construction.
Empowering Informed Decisions for Construction Professionals:
Talk.Build empowers construction professionals of all levels with the knowledge and resources they need to excel. Leverage our extensive library to:
- Optimize project management practices
- Prioritize safety protocols
- Implement sustainable construction solutions
- Integrate innovative technologies
- Navigate the evolving regulatory landscape
- Make informed material and tool selections
- Stay current on design trends
- Develop successful business strategies
Join the Conversation and Unlock Your Construction Potential:
Talk.Build fosters a collaborative environment where construction professionals can connect, share knowledge, and inspire one another. Explore our vast library of commercial construction blogs today and take an active role in shaping the future of the built environment.
Get your free webpage here
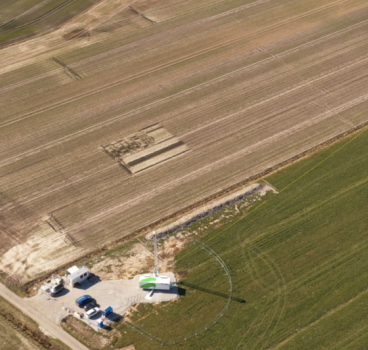
Wind-power for cranes – a construction game changer?
Wind energy, a clean and renewable resource, is emerging as a game-changer for the construction industry – with innovations that continue to surprise. By harnessing the power of the wind,...
Read moreAre empty desks a construction opportunity?
The COVID-19 pandemic fundamentally altered the way we are employed. With millions transitioning to remote work, office buildings across the Western world stand eerily empty, sparking a critical...
Read more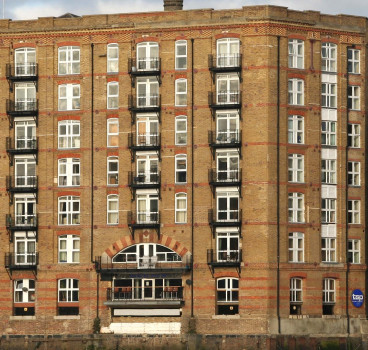
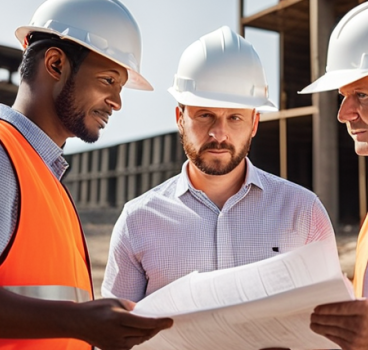
How new regulations are reshaping the construction industry
The construction industry has long been known for its focus on cost. Traditionally, the lowest bidder has nearly always secured the project, leading to concerns about cutting corners and compromising...
Read moreCombating repetitive strain injuries in construction
Repetitive Strain Injuries (RSIs) are a major concern for construction teams worldwide, affecting a significant percentage of the workforce. These injuries, caused by repeated forceful movements,...
Read more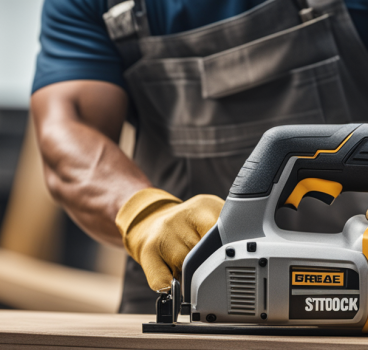
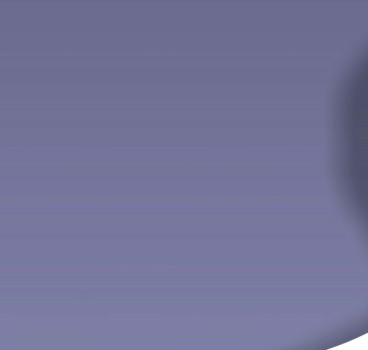
Prioritising mental health in construction
It has been an open secret for many years - construction workers face a unique set of challenges that contribute to higher rates of mental health issues compared to the general population....
Read moreThe rise of the robo-crew on construction sites
A revolution is brewing on construction sites, driven by advancements in robotics. It started to happen big time in 2020 and just four years later it is becoming a reality where tireless robots...
Read more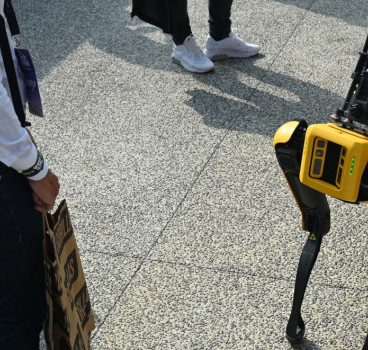
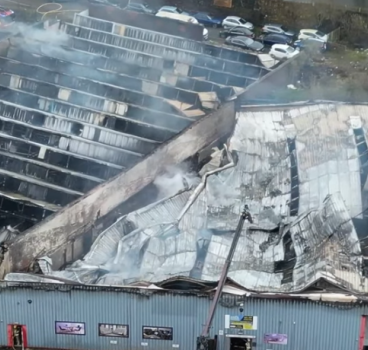
How this furniture factory could have been saved from fire
An early morning blaze at an industrial estate in Blackburn destroyed the production facilities of a local furniture upholsterer. The devastating fire swept through the unsprinklered upholstery unit,...
Read moreBuilding boom or carbon doom? The debate continues
The construction industry is booming. Cities are expanding, infrastructure needs are growing and the demand for new, energy-efficient buildings is at an all-time high. However, this progress comes at...
Read more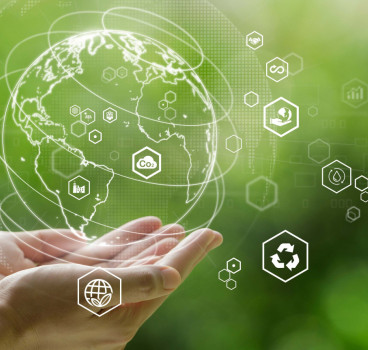
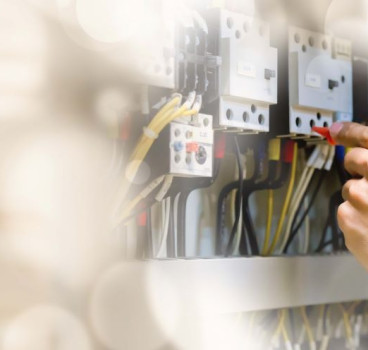
How the knowledge gap threatens the electrical industry
The electrical industry is undergoing a major change. Today’s electricians are on the cusp of a technological revolution, delivering cutting-edge solutions that are transforming the way we live and...
Read more